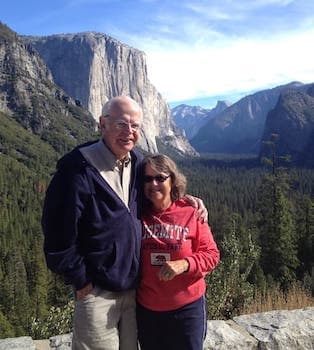
Curated with aloha by
Ted Mooney, P.E. RET
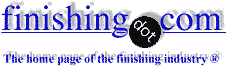
The authoritative public forum
for Metal Finishing 1989-2025
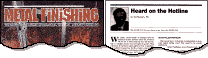
-----
Alternative to Titanium Racks for Electropolishing
I am currently using titanium racks to electropolish stainless steel which is then vacuum brazed to other components when the product is assembled. The physical contact of the stainless steel to the titanium is depositing titanium oxide on the faying surfaces which inhibits proper wetting of the braze. Are there alternatives to titanium racks that will also resist the corrosion of the current as well as concentrated phosphoric and sulfuric acid?
Jonathan FinneyMnf Engineer - Bath, New York
August 7, 2010
August 10, 2010
Hi, Jonathan. Have you tried good old copper? Not being a chemist, it surprises me that it can work, but I know of several electropolishing installations with copper racks.
Regards,
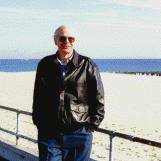
Ted Mooney, P.E.
Striving to live Aloha
finishing.com - Pine Beach, New Jersey
August 11, 2010
Copper racks would not last more than a day before it has been eroded to the point where parts would no longer be able to be fixtured. Additionally, dissolved copper would deplete the bath more rapidly as I see happening with small copper hooks connecting cathodes to the buss bar that are slightly immersed in the solution. I have heard that Aluminum is an alternative however this is also a "braze stopper." I have also heard of methods to remove the Titanium or Aluminum Oxides but all involve Hydrofluoric acid which is something I want to avoid.
Jonathan Finney- Bath, New York
Hi, Jonathan. Please try polishing a small stainless item connected via a copper hook or wire in a beaker before being too insistent that it can't work :-)
I mentioned it only because I personally know at least two production shops that use copper racks for electropolishing of stainless steel. The fact that copper erodes on the cathode side doesn't necessarily mean it will erode on the anode side. Good luck.
Regards,
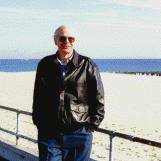
Ted Mooney, P.E.
Striving to live Aloha
finishing.com - Pine Beach, New Jersey
August 11, 2010
August 11, 2010
Copper is the standard rack material because it needs to carry a high current. The copper will gradually erode, but it will be slow. Copper is also a lot cheaper than Titanium and a lot easier to machine. Tapping can be a small problem.
I never did it, but I think that you will not have any problems from having the rack plastisol coated, which will greatly extend its life.
- Navarre, Florida
August 12, 2010
Jonathan
Have you tried phosphor bronze for your rack tips? Alloy 510.
- Colorado Springs, Colorado
Q, A, or Comment on THIS thread -or- Start a NEW Thread