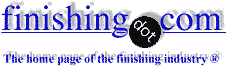
-----
Reasons for Zinc-Nickel bolts rusting? [United Kingdom]
July 23, 2010
Hello,
We are a supplier of assemblies, with aluminium corners and bolts, to the automotive industry. Our bolts are manufactured in China, with Zinc-Nickel plating and clear passivation. These bolts are then assembled in China into aluminium corners and sent to the UK to the manufacturer.
We have had not issues for three years. However one batch of the bolts was recently sent by our customer to a different assembly line in Singapore (I only mention this to highlight the different whether conditions) and a handful of bolts are showing red rust (no apparent white rust at all).
1,200 hr Salt spray test certificates of batch of bolts after plating show the bolts passed without a problem, with 8 microns of plating. The bolts are clearly plated as otherwise they would be black due to heat treatment.
Things that we are considering could have gone wrong:
1. Some of the bolts missed part of the plating process. However the plating company says this is almost impossible.
2. The sea travel of the bolts means these bolts were exposed to humid salty air for at least 60 days. But if bolts pass 1,200 hr salt spray test, this should not be an issue. Right?
3. There are thinners and other cleaning agents stored in the same area as the bolts in Singapore. Although people work in such an environment and so cannot be too bad a working condition. Could this have cause the plating to react?
We are lost as to what could be causing this issue. Any suggestions from you experience would be appreciated.
Buyer - London, United Kingdom
![]() |
Dear Anand, ![]() T.K. Mohan plating process supplier - Mumbai, India Hans, Aerospace - Yeovil, Somerset, UK |
August 3, 2010
Dear Anand,
This may be due to batch variation in zinc nickel alloy plating since you have mentioned Red rust which indicates very poor thickness of Zn-Ni alloy deposit.
Also very poor chromate or no chromate over zinc nickel alloy also would have caused the galvanic corrosion.
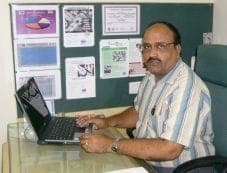
P. Gurumoorthi
electroplating process chemicals - Chennai, Tamilnadu, India
The ratio of zinc and nickel failed!
Mike Dil- Kunshan, China
August 20, 2010

Q, A, or Comment on THIS thread -or- Start a NEW Thread