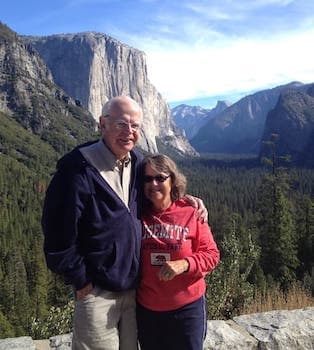
Curated with aloha by
Ted Mooney, P.E. RET
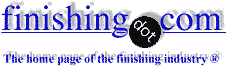
The authoritative public forum
for Metal Finishing 1989-2025
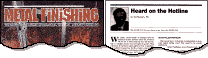
-----
Stainless steel gets rusty. Why?
Q. Hi there. I am involved in metal stamping parts, and we have supplied a SUS202 stainless steel part to our customer.
Months later, we received complaints that the parts get rusty. As far as we know, the 200 series is not as good as the 300 series, especially the 316 in terms of corrosion resistance, but is there any measurement or guideline? For example, 'the 200 series can withstand 500 hours salt spray test and the 300 series can withstand longer hours', etc.?
Besides that, what is the chemical/substance, that can cause the 200 series to get rusty faster?
Product Designer - Penang, Malaysia
July 22, 2010
July 28, 2010
A. Dear Ang ET,
First look at your own shop: No cross contamination due to using machinery which previously stamped normal steels, not fabricating SS and normal steels in the same room? Not brushing the steel with Iron brushes? A lot of corrosion problems in SS are caused by contamination the SS with Fe-particles. This topic has extensively been discussed on this website already.
Also interesting is this, which I borrowed from pfonline.com/articles/119806.html:
Never use grinding wheels, sanding materials or wire brushes made of iron, iron oxide, steel, zinc or other undesirable materials that may cause contamination of the stainless-steel surface. The use of carbide or other non-metallic tooling is recommended. Grinding wheels, sanding wheels and wire brushes that have been previously used on other metals should not be used on stainless steel. Use only clean, unused abrasives such as glass beads or iron-free silica or alumina sand for abrasive blasting. Never use steel shot, grit or abrasives that have been used to blast other materials.
Thorough cleaning prior to any thermal processing is critical. Stress relieving, annealing, drawing or other hot-forming processes can actually draw surface contaminants deeper into the substrate, making them almost impossible to remove during passivation.
Care should be taken during all thermal processes to avoid the formation of oxides. Passivation is not designed to remove discoloration and will not penetrate heavy oxide layers. In extreme situations, additional pickling and descaling operations are required prior to passivation to remove the discoloration. Controlled atmosphere ovens are highly recommended for all thermal processes to reduce airborne contamination and prevent oxides from developing.'
Then: from www.worldstainless.org I copied:
J4 is a good example -- in order to get the Ni level down to 1% Ni, and so minimize the price, it has been necessary to reduce the Cr content
to 15-16%. This is much lower than the 18.0 - 20.0% Cr specified for grade 304 and it is Cr which makes the greatest contribution towards corrosion resistance.
This means that such 200-series grades have lower corrosion resistance and are suitable for a much narrower range of applications than grade 304. This has not been well understood and there are many instances where 200-series grades have failed due to corrosion, such as when they have been used for components like handrails in exterior applications.
Another issue can be high levels of impurities such as sulfur (S) in some 200 series grades. sulfur significantly reduces resistance to corrosion such as pitting. High S is not a problem which is inherent in 200-series grades; it is a problem caused by poor steelmaking practices, and has been observed in some 200- series material made by small producers with inferior equipment and practices.
A similar situation applies to carbon (C), which is normally controlled to very low levels during steelmaking in order to avoid welding problems. High C has been measured in some 200-series material manufactured by small Asian producers and this can result in intergranular corrosion when welded structures are put into corrosion service.'
Hope this answers your question ... it could be the wrong stainless steel for the wrong application. (What we sometimes call "penny wise, pound foolish)
Good luck and best regards,
Harry
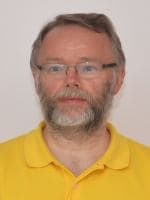
Harry van der Zanden
consultant - Tilburg, Netherlands
Q. Sir, I am manufacturing display items in ss 202. In last few months I have complaints of corrosion of ss 202. What is the reason behind it; we supply our products in matte finish.
Raminder Singh- New Delhi, Delhi, INDIA
November 29, 2013
A. Hi Raminder. It is hard to determine the actual problem without investing quite significant effort in tracking down data of all sorts, but we appended your inquiry to a similar question which was answered beautifully by Harry van der Zanden. Good luck.
Regards,
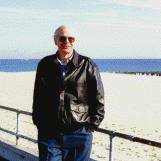
Ted Mooney, P.E.
Striving to live Aloha
finishing.com - Pine Beach, New Jersey
November 29, 2013
A. It can be a complex issue, but I'll throw out a couple quick bullet points:
* It depends on the environment. In a controlled cool and dry environment, even carbon steel will stay rust-free. In a high chloride marine environment, even well passivated 316 stainless will eventually accumulate tea staining at the very least.
* Different stainless grades have different levels of corrosion resistance. Sometimes there are other overriding factors, such as a requirement for hardness, but in general don't expect things that aren't 316 to hold up as well as 316. Plan accordingly.
* If you have iron contamination on the surface and don't remove it, it won't matter what alloy you are using, it's going to rust.
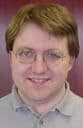
Ray Kremer
Stellar Solutions, Inc.

McHenry, Illinois
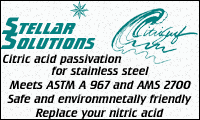
December 3, 2013
A. Rust is formed on the surface of stainless steel when a condition develops in which the metal molecules at the surface are not sufficiently alloyed with chromium to create or maintain the required oxide layer. Contrary to popular opinion, surface rusting does not occur when stainless steel is "sensitized" since the bulk of the metal has adequate chromium to prevent surface rusting; sensitized stainless steel only corrodes along the grain boundaries. Rusting phenomenon discussed in this paper is a surface phenomenon only.
The simplest condition under which rusting can occur on stainless steel is when a piece of ordinary steel is rubbed against the surface of an otherwise corrosion-resistant piece of stainless steel. The iron from the ordinary steel will rub off onto the stainless steel surface as a film of unalloyed steel, and, after exposure to moisture in the atmosphere for a few days, that unalloyed steel film will form ugly rust. This happens because the unalloyed steel film on the stainless steel has little or no chromium, so the film transforms to ordinary "red rust". Once the shallow film of iron that has "contaminated" the stainless steel surface has oxidized, corrosion stops provided the stainless steel surface remains exposed to the atmosphere and is not wetted on a nearly continuous basis. The rusted surface looks bad, but, the chromium in the stainless steel under the rust film forms a suitable corrosion-resistant oxide layer, and further corrosion does not continue once that film of unalloyed steel turns to rust.
When ordinary steel is rubbed off on stainless steel, the material which is transferred to the stainless steel is generally referred to as "free iron". This kind of "contamination" of stainless steel is also known by the misnomer of "carbon contamination". This term is a misnomer because it is not the carbon that causes the corrosion, but the unalloyed iron from which the steel is made. Corrosion of "free iron" on stainless steel is always faster than corrosion of the unalloyed steel itself because the "contamination" is anodic to the stainless steel, so the free iron on the surface corrodes to protect the stainless steel, just like zinc corrodes to protect carbon steel when zinc is used as galvanizing.
A second means of forming a rust-forming surface film on stainless steel occurs during welding when using a process that depends on flux for shielding, such as SAW and GMAW using flux-cored wire. These fluxes tend to be easy-to-remove or self-peeling, and, although the weld surface may look clean, there is a thin residual layer of iron-rich material on the surface. This layer rusts easily if the weld metal surface is not abrasively or chemically cleaned after welding. The nature of the rust that is formed is similar to that formed by mechanical contamination as discussed in the above paragraph.
- Shanghai, China
January 9, 2014
Q, A, or Comment on THIS thread -or- Start a NEW Thread