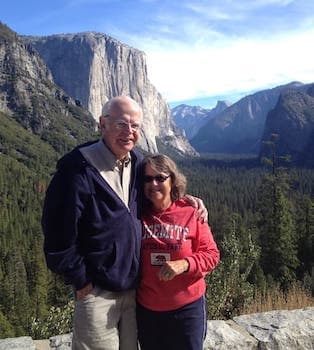
Curated with aloha by
Ted Mooney, P.E. RET
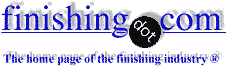
The authoritative public forum
for Metal Finishing 1989-2025
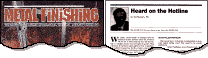
-----
Replacements for BR 127 and alocrom 1200 [England]
Hi there, I'm a student on a work placement in the materials and processes department of an aerospace company, and one of the jobs I've been tasked with is compiling a list of possible alternatives for these finishes that don't contain hexavalent chromium. I've tracked down a few possibles but am starting to hit a dead end and was hoping I could get some help.
Just some information- both are used to give some corrosion resistance as primers, and while alternatives to the Alocrom 1200 would ideally also be electrically conductive, its not vital.
student - Stevenage, England
July 22, 2010
A. Gerard,
What you need to do is quiz some manufacturers websites to see what they have to offer. So try the likes of Henkel, Trimite, Atotech, Macdermid, Chemetall, Akzo-Nobel, PPG, Deft, Randolph etc just to mention a few.
You can also try looking at the QPL for MIL-DTL-81706. This will also give you some pointers. For primers you could look at the QPLs for MIL-DTL-53022 and MIL-DTL-53030
[⇦ this spec on DLA]. These are available for free from Assist quicksearch.
Finally you want to be looking at some of the more novel technologies. There are a few out there, but you will just have to be patient and trawl the internet for them.
Good luck.
Aerospace - Yeovil, Somerset, UK
Oh! Welcome to my world.
Look up 2 things:
EW5000 primer from 3M
Boegel EPII
Then look at your qualified products.
Ask about getting materials approved.
Start crying.
Realise you can only achieve so much and settle on using BR6747-1 from Cytec instead of BR127. It's still chrome based but is at it's least non-solvent and already approved.
If you achieve this you'll still have managed more than them. Please keep asking about EW5000 though. If there are 2 of us maybe someone will finally listen.
Aerospace - South Wales, United Kingdom
July 29, 2010
July 30, 2010
I can understand the frustration! I work for an OEM and to get anything changed at all requires convincing design that it is a good idea to "go green" and to use the new technology, convince the stress department that we are not going to unduly stress the parts and cause them to fail in service (they are a thankless group), convince manufacturing engineering that it is a better system, or at least an equal one and finally convincing the shop floor that the change is for the better and although they have "always done it that way", sometimes there is a better way.
I have worked in Materials Laboratories and developed product such that they are ready to be launched on the manufacturing people only for someone in the chain to start to question the validity of the change. Back to the drawing board we go and start the process all over again!
So the average time to introduce a change that isn't forced on us by legislation can be measured in years, not days, weeks or even months.
I have started looking yet again at "green" technologies for the protection of light alloys, but don't look for my solution here anywhere in the near future!
Aerospace - Yeovil, Somerset, UK
Q, A, or Comment on THIS thread -or- Start a NEW Thread