|
Unlike 316 (I think), 304 SS can become ferromagnetic from cold working - wire drawing, rolling, centerless grinding, shot blasting, heavy polishing, are some mentioned on the internet. Check this thread.
www.finishing.com/454/35.shtml
Chris Owen
- Nevada, Missouri, USA
July 27, 2010
July 27, 2010
Dear Guru Deep.
As this is a voluntary forum and even for free, you cannot expect an immediate reply. I hope the following information is useful to you, in order to widen your understanding, you should do additional research:
Summarizing: From the composition: Yes, this is SS. Normally the SS 3-4 is non-magnetic. An extreme cold working or heat treatment could make is magnetic.
Yes, This can influence the corrosion properties as well.
So, If I was in your place, and till now you always received non magnetic material, I would be suspicious about this supply. Your should have a very good explanation and guarantee why it is now suddenly magnetic and that this delivery is not different in behaviour from earlier deliveries and about what happened which made it different from earlier deliveries. (Rolling, casting and heat treatment processes can have an influence on magnetic properties of this type of stainless steel)Having detected such a difference, I only would take the risk in using it for "low risk" applications after thorough testing the final product compared to the original stainless steel supplies you used and even that isn't an absolute guarantee. If it is for critical parts, you shouldn't and couldn't take a risk and of course you have to tighten your specifications as well.
There has been an earlier discussion on this topic in this forum, see:
www.finishing.com/333/03.shtml
Although not directly referring to your problem, but comparable:
www.finishing.com/112/70.shtml
For your further information (with thanks to Pat Doyle -see: http://lists.contesting.com/_towertalk/1996-11/msg00136.html)
(What follows is copied from this site):
Stainless steel is a ferrous (iron based) alloy. The American Society for Metals (ASM) defines stainless steel as an alloy containing at least
10% chromium (Cr) (with or without other elements). Few of the alloys contain more than
30% Cr or less than 50% iron (Fe). Cr is the element that makes the stainless steel more resistant to rusting and staining than plain carbon or low-alloy steels. Other elements are added to give specific properties.
There are four metallurgic categories for stainless steel: 1) martensitic; 2) ferritic; 3) austenitic; 4) precipitation-hardened. The most common types found in general use are martensitic and austenitic. I will not address the less common types.
Austenitic stainless is non-magnetic. Martensitic stainless is magnetic.
Nickel (Ni) is found in austenitic stainless and is makes it non-magnetic. It has to do with the alloy structure and where the various elements of the alloy end up in that structure.
Martensitic is stronger and harder than austenitic, primarily because it is heat treated. The heat treating causes the alloy's structure to form such that it is not magnetic.
Alloy 304 is an austenitic stainless and has the widest range of applications and is available in a variety of forms for exterior architectural applications. If you encounter stainless steel, it is most likely 304. It possesses excellent resistance to corrosion from exposure to weather. It is non-magnetic.
304L is a low carbon version having slightly higher corrosion resistance. This is a good choice if the piece is to be welded. Welding reduces stainless steels' corrosion resistance. Carbon will "steal" Cr to form Chromium Carbide at welding temperatures (remember that Cr is what makes stainless corrosion resistant).
Best regards,
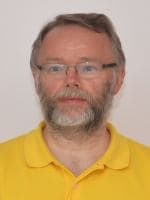
Harry van der Zanden
consultant - Tilburg, Netherlands
|