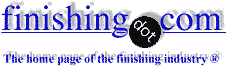
-----
Aluminum hard-coat anodizing: is thicker better?

Q. We are using extruded aluminum parts (6063-T6) that carry cardboard cartons for sorting.
One extruder says that a thinner hardcoat is best. Our other vendor claims that thicker is best for wearability. Wear will come from pushing cartons off the moving "deck" made from these extrusions.
R&D Mechanical Engineer - Mason, Ohio, USA
July 16, 2010
A. Two mils (0.002" or 50 µm) is generally recognized as the optimal hardcoat anodize thickness. Most anodizing specifications use it as the default. Thicker hardcoat can start to get soft and powdery. Thinner hardcoat will offer less wear protection.
Chris Jurey, Past-President IHAALuke Engineering & Mfg. Co. Inc.

Wadsworth, Ohio
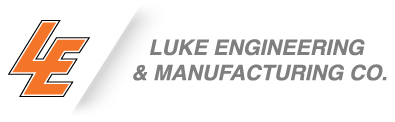
A. The smaller pore is what makes "hardcoat" called hard, it is not really any harder, but you do have increased wear resistance. The pore is smaller at the lower thicknesses and therefore wears longer at the lower thickness, the pore is conical and gets larger as the thickness builds and it abrades off faster at the higher thickness.
Hardness can be measured on the Knoop scale by bringing the diamond in ON THE CROSS SECTION, there, again, it has been documented in the scientific journals that a "harder" measurement is observed at the lower thicknesses.
The terms hardcoat and regular anodizing are thrown around recklessly in the industry. Five shops in the same county showed me 5 different colors and 5 different Taber Abrasion results on the same alloy and thickness.
You need to do some testing and then write some specific specifications.
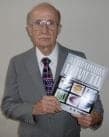
Robert H Probert
Robert H Probert Technical Services

Garner, North Carolina
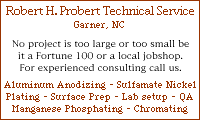
Q, A, or Comment on THIS thread -or- Start a NEW Thread