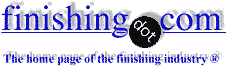
-----
How to know when it's time to discard a "P2" Ferric sulphate solution?
July 15, 2010
We run an aluminum panel chemical conversion coating operation and are interested in developing the best way to determine when a "P2" Ferric sulphate solution is degraded to the point where it is time to discard. In the past this has been done with mostly gut feel, but we want a way to test and track the tank's status using tracking charts.
I sent some samples out and a few results that came back that were promising, specifically the dissolved aluminum in mg/L and also conductivity in µmohs/cm. The idea going forward was to track these two characteristics to see how they changed.
The lab test compared a fresh batch sample (prepared by the testing lab) and compared that to our actual process sample which was 6 months old. The results were as follows
Aluminum test results
Method..................EPA 200.7
Param...................Aluminum
Units...................mg/L
Rep Limit...............10
Result (Lab Sample).....23.5
Result (Process Sample)..1,530.0
Conductivity test results
Method..................SM 2510B
Param...................Conductivity
Units...................µmhos/cm
Rep Limit...............1
Result (Lab Sample).....41,000,000.0
Result (Process Sample)..13,100,000.0
They performed many other tests but these two test's showed the most change from fresh lab sample to 6 month old process tank.
Does anyone have any suggestions about the path we are on? Any alternatives?
Thank you
Engineer - Marion, Virginia, USA
I doubt that any meaningful scientific work has been done, and even then, every shop is so different in the alloys it processes that any set of parameters could not cover the universe. That type of deox last a very long time. Questions start earlier in shops that drop parts and/or run 2000 alloys. In Aluminum How-To, I suggest taking a 5 gallon bucket out, making a 25%/vol add, then in another 5 gallon bucket make a new solution, then bring three panels down the line: one in the tank, one in the 25% add, and one in the new make-up. then chromate all together. Then judge by the naked eye, and/or corrosion test. This will tell you a lot more than any lab chemist.
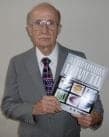
Robert H Probert
Robert H Probert Technical Services

Garner, North Carolina
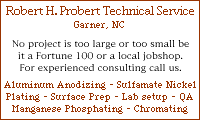
July 16, 2010
Q, A, or Comment on THIS thread -or- Start a NEW Thread