Curated with aloha by
Ted Mooney, P.E. RET
The authoritative public forum
for Metal Finishing 1989-2025
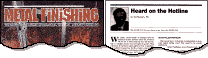
-----
Pulse plating rectifier benefit for rotogravure cylinder plant
July 16, 2010
PLEASE SOMEBODY REPLY TO THIS QUESTION :--
NOWADAYS WE ARE PRODUCING THE ROTOGRAVURE CYLINDERS (FOR CHEMICAL ETCHING,ELECTRONIC ENGRAVING AND INDIRECT LASER ENGRAVING) THROUGH 05% RIPPLE RECTIFIER WITHOUT THYRISTRISED (ON continuous PLATING) FOR NICKEL, SOFT COPPER,HARD COPPER AND HARD CHROME (ACI BASE) SO, CAN WE CHANGE OVER ALL BATHS TO PULSE PLATING RECTIFIER ?
IF YES THEN WHAT BENEFIT CAN WE GET THE ? LIKE QUALITY OF PLATING, POWER SAVING OR ANY OTHER.
Because PRESENTLY USING RECTIFIER CAPACITIES ARE 10 /12/15 VDC AND
500/1000/2000/2500/3000/4000/5000/6000 ADC (AMPERE CAPACITIES ARE DEPENDING UPON THE BATH CYLINDER PLATING CAPACITY )
EXPECTING YOUR FEED BACK SOON.
REGARDS,
RAVI FROM INDIA
RAVI JOSHI
plating shop employee - MUMBAI, INDIA
|
There are select applications where pulse plating has benefits. Periodic reverse also has some applications that have good benefits. The problem is that it is not a silver bullet that solves all problems. In fact, it generates major problems for most since there are specific voltages/amperages for the application. Few people know that much about it except those that have researched very very specific applications. Even the manufacturers of the high price equipment do not know the perfect "window" for your varied uses. Those with the knowledge are not prone to sharing information other than the most elementary data.
It is my understanding that a lab sized test unit does not scale up to production size without additional research.
PS, the equipment used to be very expensive.
James Watts
- Navarre, Florida
Hi Ravi,
in the past 8 years the major companies in rotogravure machinery/plating industry has done some research of the benefits from pulse plating and other techniques which is widely used in the electroplating industry, however, at the end some of them has been successful, others not and this is valid for the pulse plating on rotogravure cylinders. For sure the microcrystalline structure has been very improved, but it was not very stable and also the rectifiers are more expensive. On of the techniques which are now in use is
- Copper deposition with ultrasound and insoluble anodes in which the copper is externally dissolved with copper oxide and fed by setting up some online analysis method. Worldwide exists only approx. 4 processes in use with this technique
- Copper deposition with insoluble anodes and externally dissolving of copper. This technique came up approx. 2.5 years ago and has an increasing demand due of the fact, that particles which are caused by copper nuggets does not cause quality problems onto the cylinders which caused pores and/or roughness. Also the microcrystalline structure is more stable and a re-crystallisation during storage time is very minimized.
Please be aware that rectifiers for hard chromium plating, especially catalyst ones, have a ripple less then 3%.
Cheers, Dominik
Dominik Michalek
- Melbourne, Australia
|
Disclaimer: It's not possible to fully diagnose a finishing problem or the hazards of an operation via these pages. All information presented is for general reference and does not represent a professional opinion nor the policy of an author's employer. The internet is largely anonymous & unvetted; some names may be fictitious and some recommendations might be harmful.
If you are seeking a product or service related to metal finishing, please check these Directories: