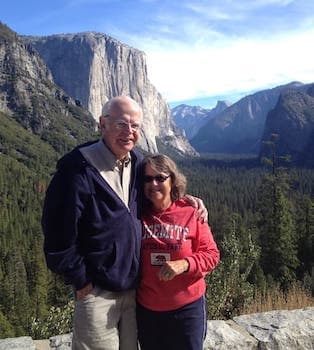
Curated with aloha by
Ted Mooney, P.E. RET
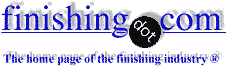
The authoritative public forum
for Metal Finishing 1989-2025
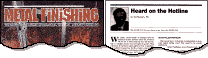
-----
Preventing Tarnish on Gold Plated Silver & Brass
Q. Hello there
I'm know this is an old thread but I just find it cause i'm new in this, i have My own fashion Jewelry workshop, we are casting pieces in brass and I bought a small electroplating machine from Legor, I work with a palladium solution from Legor with 3 gr per liter and a gold solution with 4 grams per, following the dealer instructions. I'm giving a 0.2 micron of Paladium to the pieces and then 0.5 microns of gold. But I still feel the pieces turn dark SO fast, any advice?
Shop - Medellin - Colombia
August 23, 2023
⇩ Related postings, oldest first ⇩
Q. I'm working on restoring the gold-filled or gold-plated trim on vintage fountain pens, and I have a couple of questions about gold plating.
1. Is it important to pre-plate brass with nickel to prevent migration? I'm pretty sure from what I read here that copper would absolutely migrate into gold, but will brass have the same problem? Is it possible to gold plate directly on brass without risk of discoloration due to this migration effect? Is there some thickness of gold plating that would virtually eliminate any migration of the brass to the surface of the gold?
2. Is there a chart available that lists the voltage ranges and anode materials that should be used with each of the common plating metals? I'm trying to determine what pen plating setup to create, and I'd like to know what voltages and anodes I'd need for the above-mentioned nickel barrier plating and for the gold finish plating.
Thanks!
Daniel Kirchheimer- Monmouth Junction, New Jersey
1999
A. Daniel, if I am understanding correctly you wish to plate over a brass substrate. If you are not currently permitted this is a problem. First a copper cyanide strike followed by copper plating (acid copper). Then the copper must be activated followed with bright nickel. Then the gold. No matter how thick the nickel or gold plate is, the brass (zinc/copper) will migrate without the nickel. The copper allows the nickel to adhere.
You may want to pursue a brush plating kit.
Bill Hemptech svc. w/ chemical supplier - Grand Rapids, Michigan
Multiple threads merged: please forgive chronology errors and repetition 🙂
How thick must gold plating be?
Q. I work for a jewelry company that buys from overseas factories. We have gold-plated silver and gold-plated brass products that are tarnishing, apparently due to insufficient plating and the presence of sulfur ⇦ this on eBay or Amazon [affil links] in the packaging. I have a few questions: First, is there a minimum thickness that would ensure plating didn't tarnish and lasts a long time (i.e., years)? Would this be different for gold-plated brass vs. gold-plated silver? How about rings versus pendants? Would e-coating be a good solution? I worry the coating might peel off and look odd after some time. Thanks!
Mike O'DonnellJewelry Manager - Norwalk, Connecticut, USA
July 1, 2010
by Reid & Goldie
-- hard to find & expensive; if you see a copy cheap, act fast!
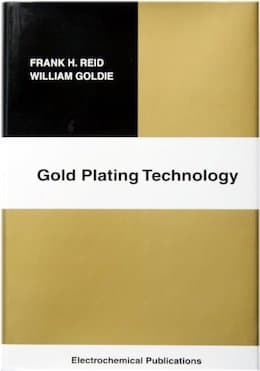
on eBay or
AbeBooks
or Amazon
(affil links)
A. Hi Mike. Yes, insufficient thickness, and sulfur in the packaging, are both problems. Two obvious conditions that can lead to tarnish are porosity due to the gold wearing away or having been too thin from the get-go, and diffusion (molecular level intermixing over time) of the gold with the silver or brass such that the surface is no longer pure gold. While the obvious answer to both problems can be very thick gold plating (gold plated pocket watches have easily lasted a century), gold is very expensive, so other answers to the wear problem and diffusion problem have been offered.
Some of the answers to the wear problem have included:
- The application of titanium nitride in addition to or in lieu of gold plating because it is hard, relatively cheap, and looks very much like gold.
- E-coating or other clear coating that can let the gold show through, while increasing the time before it wears away. Properly done, it will not peel off.
The answer to the diffusion problem can be a barrier layer of nickel or other metal which is more resistant to molecular diffusion.
How thick the gold should be is complex because wear on rings might be a hundred times as severe as wear on pendants, and because it depends on whether gold thickness or another material are your primary barriers against both wear and diffusion, and what standards you want to hold yourself to in providing real vs. fake.
Those old pocket watches might have had 200 microns of gold plating, super-high quality heirloom plating on $10,000 luxury watches today is about 20 microns, very high quality costume jewelry is often about 2-1/2 microns, most "nice" quality costume jewelry is probably 1 micron, but thickness can go down as low as 1/10 of a micron on really cheap stuff or where TiN or clear coating are providing the wear resistance. Good luck.Regards,
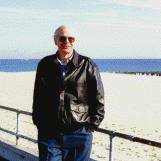
Ted Mooney, P.E.
Striving to live Aloha
finishing.com - Pine Beach, New Jersey
A. Silver, copper, and zinc will walk right through gold with time and/or temperature. You must have a diffusion barrier of nickel or palladium between the silver, and/or copper, and/or brass.
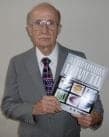
Robert H Probert
Robert H Probert Technical Services

Garner, North Carolina
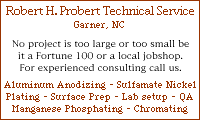
A. If gold is plated directly on silver, copper, brass, etc., these metals will migrate up through the gold and produce tarnish on the surface. The thicker the gold, the more time it will take but, in my experience, it will eventually happen. For this reason, an adequate thickness of nickel is commonly plated underneath the gold to act as a barrier to this migration. The gold, itself, should not tarnish unless it's of a very low karat.
I would first suspect the nickel as being too thin or not being there at all.
- Nevada, Missouri, USA
A. By federal code gold electroplated jewelry needs at least 7 micro-inches thickness of gold. Heavy gold plate and Vermeil must be at least 100 microinches thick. Very often jewelry made in the third world does not meet these standards. To prevent tarnish a barrier layer of nickel or palladium should be plated over brass and silver before gold plating.
Neil BellAlbuquerque, New Mexico
A. I used to work for a fine jewelry Co. in Newark,NJ.
We developed and marketed 18 kt gold electroplate brass jewelry with lifetime warranty. At that time there was no standard (astm, mil-spec, etc.) that met our requirements. We developed our own.
Good Luck,
- Mays Landing, New Jersey, USA
July 22, 2010
Q. Would you be happy to share what you found to work?
I am curious if you used a barrier plate (today that would have to be palladium in the uk as nickel is illegal in jewellery) and if so, how thick the barrier was?
And indeed how thick the 18k gold plating itself was?
best,
- uk
July 4, 2023
A. Hi Ruby. We'll try to advise Hamilton of your questions, but he hasn't posted on this site for going on 9 years, so we're not confident.
Assuming we don't reach him, you can probably increase interest & participation from the readers if you tell them about your own situation. Some people rely on clear coats, others rely on TiN and similar PVD coatings, and still others rely on thick, hard, gold. That jewelry manufacturer in Newark was famous for their tri-color (green, pink, yellow) gold jewelry items. Thanks.
Luck & Regards,
Ted Mooney, P.E. RET
Striving to live Aloha
finishing.com - Pine Beach, New Jersey
Gold plating musical instrument mouthpieces
Q.
My company in Winter Park, Florida, is often asked to gold plate mouthpieces for musical instruments. It has been my habit to silver plate the brass mouthpiece before depositing my gold. My question is this: is it acceptable by industry standards to do this? Will silver migrate into the gold layer? If it does, is that bad? I notice that manufacturers of church accessories often plate gold directly over sterling silver chalices and ciboriums, etc.. I've been doing this for thirty years and haven't had any complaints from my customers, but after a conversation with another metal finisher here in Orlando, I've been having second thoughts. Can you give me any guidance in this matter?
Thank you for your time,
owner - Winter Park, Florida, USA
April 7, 2012
A. Hi David.
If a process has been working fine for you for 30 years, pragmatism suggests that you not change it :-)
Mouthpieces never get above room temperature or body temperature, so diffusion is slow. They are not soldered, so no concerns of intermetallics messing things up. They are not electronic components where ultra-low contact resistance must be guaranteed. They are not fine jewelry where the slightest off-color could be a killer issue. Adding a nickel layer would be adding many potential complications, including possibly exposing people to a nickel surface (some people are genuinely allergic to nickel and others may be paranoid about it).In short, it's working fine for your application so don't change it ... but don't go lecturing the Orlando shop that they don't need a nickel barrier -- their application is probably different, and they they probably do need it :-)
Regards,
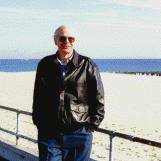
Ted Mooney, P.E.
Striving to live Aloha
finishing.com - Pine Beach, New Jersey
A. I was just looking at a piece of 60+ year old Tiffany Vermeil.
It still looks like new.
Will silver migrate through gold plating if there is no nickel barrier? Yes. But if the gold plating is done well and thick enough, it won't happen in a lifetime.
I'm guessing, and it's only a guess, that at ambient temperature, the migration of silver through gold is no more than a few microns per year, so if you're plating, say 50+ microns of gold, your original customer will never have a complaint.
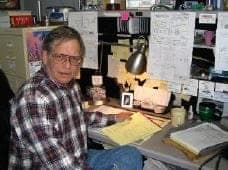
Jeffrey Holmes, CEF
Spartanburg, South Carolina
Gold plated brass jewelry is tarnishing in a week
Q. We recently started manufacturing brass jewelry. And a lot of our pieces need to be gold & rhodium plated. We are seeing a lot of gold plating starting to tarnish within one week of plating. The rhodium plating remains fine. What could be the reason? We have the following plating process:
- Polished brass jewelry is cleaned.
- Brass jewelry is plated with Alkaline copper
- Pieces are then plated with Acid copper. This plating is thick micron plating.
- Pieces are then plated in silver strike solution
- Pieces are plated with silver micron (cyanide based)
- Pieces are then plated with palladium (flash)
- Then finally gold plated (flash)
- Lastly rhodium plated.
Thanks and I look forward to feedback.
- Mumbai, INDIA
June 13, 2013
A. Hi Pushpak,
Possible causes are:
1. Gold bath contamination (metallic and/or organic).
2. Poor water rinsing after gold plating.
3. Gold deposit porosity.
4. Storage environment.
5. Metal migration from substrate.
Regards,
David
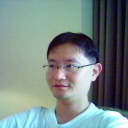
David Shiu
- Singapore
A. Hi Pushpak. The only thing I'd add to David's answer is that, while your process is meticulous, with 6 different layers of plating ... If I'm understanding you correctly and parsing your phrasing the way you intended, a micron of copper and a micron of silver is hardly thick plating. I'm not sure that either is even non-porous.
Regards,
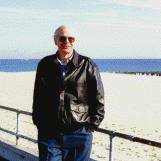
Ted Mooney, P.E.
Striving to live Aloha
finishing.com - Pine Beach, New Jersey
3 Micron Gold Plating on Brass Jewellery
Q. We are an export house based in India and we are working on base metal of Brass.
We face a problem at the time of plating and polishing. We are making very heavy pieces of Brass Jewellery. When we try to plate 3 micron gold on the same there are lot of scratches visible; these scratches are from the high glaze finish polish that we have done.
After polishing we have done silver plating up to 2 microns and re-polished the same. We do the silver plating again up to 2 microns and then deposit 3 microns of gold on the same.
However, the final result is not very good as the scratches are still visible and also the gold tarnishes after a couple of days.
We have been outsourcing the polishing and our plater advised to do silver plating first as silver is soft and would form a layer on the surface thus hiding all the scratches, etc. -- but this has not helped yet as the scratches are still visible.
What could be the reason for the Gold Tarnishing, and also how can we overcome the Scratches formed by the emery paper at the time of polishing?
- India, Delhi, New Delhi
January 4, 2014
A. Hello Rahul,
Silver plate is not considered a diffusion barrier. I anticipate the fact that nickel can't be used because you are plating jewelry? Without a diffusion barrier you will continue to see tarnishing. Another advantage of a good barrier plate is that it provides good leveling characteristics, which covers imperfections like fine scratches. If nickel cannot be used, have you considered White Bronze? Palladium is also a good barrier plate, but is expensive and would play havoc on your bottom line. I am a little surprised that you are seeing tarnishing in a few days with 120+ microinches of gold thickness. With that thickness it usually takes longer for tarnishing to appear. In summation, consider a good barrier plate between the brass and the gold that has good leveling characteristics. Good Luck.
Process Engineer - Malone, New York, USA
A. Are you doing rack plating or barrel plating? if you are barrel plating then you need to add some filler such as copper or glass beads that will keep the parts from scratching each other.
Mark is correct in that you need a barrier layer to keep the gold from diffusing into the substrate. if you can't use nickel then try iron or cobalt.
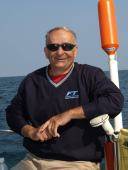
Pat Mentone
St Paul, Minnesota
Q. Hi,
We have been advised by another player to follow the other process as below:
Copper cyanide
After copper cyanide, rebuffing of the jewellery
Then acid copper; they say this form will form a hard layer
After copper acid do cobalt or nickel plating
And after this 3 micron gold plating
Now if this process is good enough or is there anything else that we should keep in mind like the duration between the 2 processes and if after Nickel or Cobalt do we need to give some kind of sulfuric acid bath or something so there is better bonding?
jewellery - New Delhi, India
January 12, 2014
A. Hello Rahul,
Before Acid Cu plate you will want to employ these steps.
1) Soak clean
2) Electroclean
3) Double cascade rinse
4) 5-10% Sulfuric acid dip
5) Acid Cu plate
6) Double cascade rinse
7) 10% Sulfuric acid dip
8) Rinse
9) Ni or Co plate
10) Double cascade DI Rinse
11) Acid activate
12) DI rinse
13) Au plate
The reason for a soak clean and an electroclean is that the soak clean will loosen the soil on the part and the electrocleaner will blow it right off. You may already be doing this after the buffing process. Moving farther down the line, you will want to get into the Au bath within 90 seconds after the acid activate. Ni has a tendency to go passive if there is a delay going into the Au.
Good Luck.
Process Engineer - Malone, New York, USA
(you are on the 1st page of the thread) Next page >
Q, A, or Comment on THIS thread -or- Start a NEW Thread