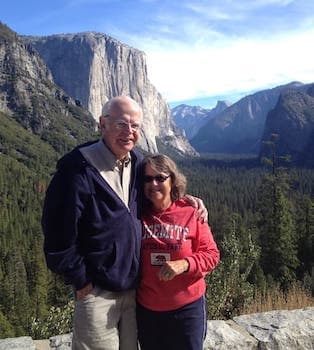
Curated with aloha by
Ted Mooney, P.E. RET
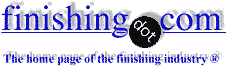
The authoritative public forum
for Metal Finishing 1989-2025
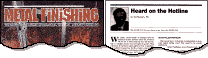
-----
Heat treated 420 stainless steel passivation failure causing severe black corrosion
We are having problems passivating heat treated 420 stainless steel to QQP35C type 2 passivation.
The parts are coming out black with severe corrosion however within the same batch other heats of material are coming out fine.
The material is to spec and heat treats to hardness.
The parts are vacuum heat treated, finish ground, (in some cases glass bead blasted), then cleaned in solvex solvent and finally passivated.
We have had 3 contractors do this job, one has had no problems and has been doing the job for years without issues but has now gone out of business thus we can no longer use them. The other two have had this failure and cannot explain why.
Can anybody provide advice as to why this issue might be happening?
Engineering Director - Melbourne, Victoria, Australia
July 1, 2010
July 6, 2010
Hi, Ash. You might consider citric acid passivation if you are having too much trouble with nitric acid passivation. I am not sure that I believe it 100%, but some people feel this is due to inadequate cleaning. Oils combined with strong nitric acid can create powerful organic etchants. Ask your passivation shop to try electrocleaning the parts if it doesn't violate your specs.
Regards,
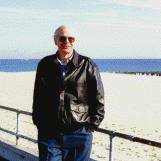
Ted Mooney, P.E.
Striving to live Aloha
finishing.com - Pine Beach, New Jersey
July 6, 2010
Some of the 400 series stainless can be a real problem and can vary on the same rack or basket.
Citric does not seem to suffer this problem, so for 400 series SS, I would recommend switching to citric passivation.
Check the posts on this subject at this site from a couple of years ago. There was some good information brought out in them.
- Navarre, Florida
Thanks for the advice I will try alternate pre cleaning methods however we are stuck with QQp35 C
Regards Ash
- Melbourne Australia
July 12, 2010
August 13, 2010
We had variation within a passivation batch. A quick check with a XRF gun shown a difference in chemistry in the steel, particularly in chromium. This must have been due to a material mix up with the supplier. Check your steel.
Jenny Bibby- United Kingdom
Q, A, or Comment on THIS thread -or- Start a NEW Thread