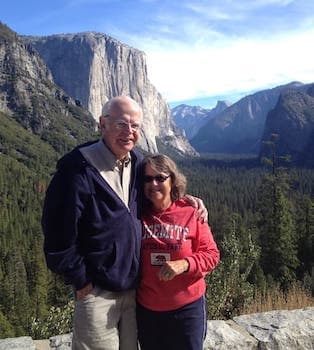
Curated with aloha by
Ted Mooney, P.E. RET
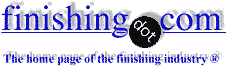
The authoritative public forum
for Metal Finishing 1989-2025
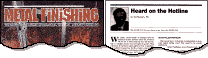
-----
Accepted method for checking thickness of pure tin plating
Q. One of our customers is doing thickness monitoring on their pure tin plated parts. In-house checking is done using XRF machine which we check both front and back side with an average of 11-12 microns. But on the customer side, which is using a cross-section to check the thickness, the thickness range is 8-40 microns.
Can you please help identify the difference of each method and which is more accurate. Is it standard to do cross-section to check the plating thickness?
Please advise.
Plating Engineer - Singapore
July 6, 2010
A. Hi, Alfred. Cross-sectioning is almost always considered the "referee" method except for too-thin coatings where smearing is inevitable. Although it's possible to do it poorly and thereby get inaccurate results, you can't argue with a good cross-sectioning.
Cross-sectioning, however, is a destructive test which can only be used on sample parts, , whereas XRF can be used on production parts without harming them. A portion of your problem may be inaccurate calibration of your machine, and a portion of the problem may be testing at different points on the part (the thickness of electroplated coatings can vary dramatically across a part).
Regards,
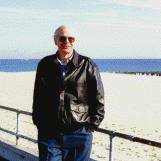
Ted Mooney, P.E.
Striving to live Aloha
finishing.com - Pine Beach, New Jersey
July 6, 2010
If this part has sharp edges, it could easily have 4 times the amount of plate than the center of the part. I would first get a new set of certified standards for your XRF. Then I would ask to see their specimen mount that had 40 mills of plate. It is easy to grind ( wet sand off another 100 mills of the entire mount and re-polish, etch/stain and read the mount. If there is a major difference from the first readings, then the customer is not doing a good job in the sectioning of the part for the sample. I can make the sample read nearly anything that you want by choosing where I cut the sample from.
James Watts- Navarre, Florida
July 6, 2010
Q, A, or Comment on THIS thread -or- Start a NEW Thread