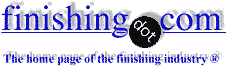
-----
Electro polish, Passivation in Nitric Acid, Electroless nickel plating
Hello Experts:
I'm impressed about your experience, and I want to submit a question.
Electropolish
Passivation per Nitric Acid
Electroless nickel plated
Can this be a good formula to avoid corrosion issues on 430F SS?
Design Engineer - Chihuahua, Mexico
June 29, 2010
Hi, Carlos. You can either electropolish or passivate the stainless steel. If you have electropolished it, there is no advantage to subsequently passivating it because the electropolishing leaves it very well passivated. But still, it's a grade 4xx stainless steel and will not be as corrosion resistant as 3xx.
Electroless nickel plating will outperform 430 stainless steel in some environments, but probably not all.
Regards,
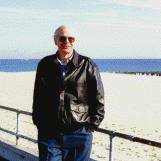
Ted Mooney, P.E.
Striving to live Aloha
finishing.com - Pine Beach, New Jersey
June 30, 2010
First of two simultaneous responses -- July 1, 2010
Hi Carlos,
If your main concern is corrosion resistance, perhaps you should consider a 300 series stainless steel instead (310, 316). Though softer, their nickel content make them very resistant. If you also need hardness, you may consider a hardcoating over said steels. Options include PVD coatings such as Titanium nitride, Titanium-Aluminum nitride, Chromium carbide and other. These are extremely hard and friction resistant but, since they are very thin, when applied over soft substrates they cannot take high loads.
If this is not enough, there are nickel or cobalt alloys such as Stellite, Inconel, Incoloy that provide supreme mechanical and corrosion resistance.
Good luck,
Monterrey, NL, Mexico
Second of two simultaneous responses --
Electropolishing and passivation both lend to corrosion resistance in stainless steel, but by different mechanisms.
Electropolishing smooths the metal surface, the current removes all the microscopic peaks in the metal. Corrosion is an electrochemical process, and takes place mostly at those same peaks. This is why an electropolished surface is corrosion resistant.
Passivation (via nitric or citric acid), on the other hand, is the preferential removal of iron from the surface, which produces a chromium layer that becomes a protective chrome oxide.
Combining both effects, electropolishing followed by a citric acid passivation, gives you surface that is smooth and has the improved chrome oxide layer, boosting the corrosion resistance even more. However, in most situations the corrosion resistance from one or the other process is sufficient.
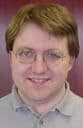
Ray Kremer
Stellar Solutions, Inc.

McHenry, Illinois
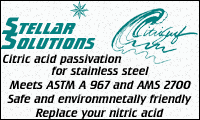
July 1, 2010
Q, A, or Comment on THIS thread -or- Start a NEW Thread