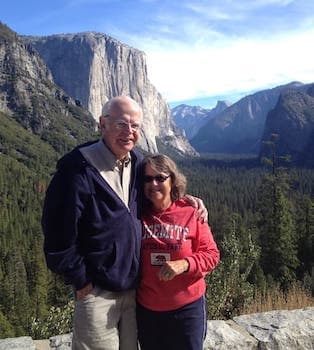
Curated with aloha by
Ted Mooney, P.E. RET
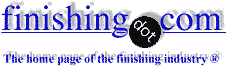
The authoritative public forum
for Metal Finishing 1989-2025
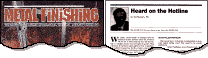
-----
Cost Implications of Specifying Hard Coat Anodized Finish
June 28, 2010
Hello and thanks to all the industry experts out there.
I have already learned a tremendous amount from observing this forum, and I am hoping to gain some additional insight.
I am an engineer currently specifying the anodic coating of aluminum parts and want to know what the cost implications are for using a specification such as MIL-A-8625 Type III Class 1, unsealed, or SAE AMS2469, unsealed (vs. other types of coatings and architectural spec anodized finishes).
In the application, we are concerned primarily with dielectric separation, adhesion, and durability -- general corrosion resistance is secondary. The aluminum parts will be 6061-T6, extruded and machined, generally less than 10" max. dimension.
I would like to know if there is a high $$ premium and/or lead time for this type of coating associated with the testing requirements.
Should we indicate performing only the testing we feel is appropriate and waive the rest? (i.e. only perform thickness and abrasion resistance tests) Or is that a recipe for trouble down the line?
Thank you,
architect/engineer - Washington, DC, USA
Hardcoat or Type III anodize is a much thicker, denser version of a commercial or Type II anodize. As such, hard anodize provides superior dielectric, wear, and corrosion resistant properties. However, due to the increased electrical power and processing time requirements, hardcoat is also much more expensive. This added cost is not primarily a function of the testing requirements but rather the differences in processing parameters.
Chris Jurey, Past-President IHAALuke Engineering & Mfg. Co. Inc.

Wadsworth, Ohio
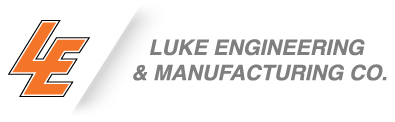
July 1, 2010
Q, A, or Comment on THIS thread -or- Start a NEW Thread