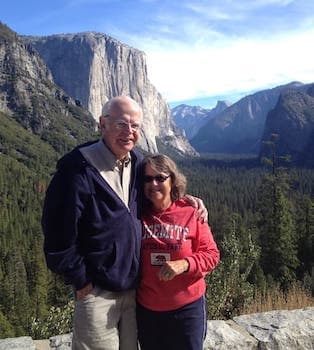
Curated with aloha by
Ted Mooney, P.E. RET
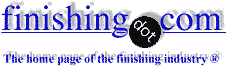
The authoritative public forum
for Metal Finishing 1989-2025
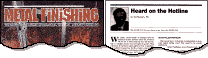
-----
Nitride finish on hydraulic cylinder rod
We manufacture snowplows and are moving towards nitride finished cylinder rods (instead of chrome). I trust our cylinder vendors, but always prefer to know everything I can about a process before I dive in.
Our vendor will most likely use pre-nitrided rod with a nitrided case depth of .3mm (.012"). I'm looking for corrosion resistance (#1) and lubricity as a bonus.
Is there a relevant SAE spec to call out? I looked at AMS2753 C, but that is a much thinner case. I suspect the pre-nitrided rod is some proprietary spec (QPQ, Tufftride, etc.).
I want a spec on my print - any suggestions what I should be requiring? I hate to put Nitride Finish, case depth .012" That's too wide open to interpretation.
Thanks
Design Engineer - Cleveland, Ohio, USA
June 25, 2010
July 16, 2010
Unfortunately there are no automotive standards from SAE for nitriding, only the aerospace standards like AMS 2753, AMS 2757, AMS
2759/12, etc. Generally speaking, there really aren't any consensus standards (other than the aforementioned documents) for specifying nitriding. I recommend that you use ISO 15787 "Technical product documentation ˜ Heat-treated ferrous parts ˜ Presentation and indications" for specifying the requirements. Section 6.6 pertains to nitriding and nitrocarburizing. For your particular case, you should specify the compound layer thickness (CLT), also called the white layer, as well as the nitriding hardness depth (NHD).
As an example, the drawing would state "nitrocarburized" with a specification for CLT such as "CLT = 12 +6/-0 μm" and "NHD HV0.3 = 0.3
+ 0.1 mm". The HV0.3 means Vickers hardness using 0.3 kgf load. NHD is usually defined as the point where the hardness is 50 HV0.5 over the actual core hardness (DIN 50190-3 and ISO 15787 both reference this value). You may want to also specify the black oxide layer thickness that is the outermost layer (usually < 3 μm) and/or the amount of porosity in the CLT.
Automotive component/module supplier - Michigan, USA
Scott, most nitriding is done as a cathodic-arc process, yielding a relatively rough surface, as does the controlled cracking of plated chrome, as viewed under high magnification (1000x); and thus not friendly to seals.
A more better solution would be a chrome replacement technology applied using HVOF technology which yields a dense (1% porosity), hard (75 HRc), continuous coating. Applied at a 0.014" residual finish on the O.D. after diamond grinding to a 16 Ra (glass = 8 Ra) surface finish.
- Fairburn, Georgia, United States
September 28, 2010
Dear mr Scott Moorman, Toby Padfield, Craig Schindler
instead of nitriding, pack or paste boronizing is a good alternative to improve on corrosion and wear resistance; the diffused case depth achieved can be varied from 50 to 100 microns in boronizing, the treatment temperature is higher 750- 1000 deg C in boronizing, so precaution for warping and dimensional tolerance is to be taken care before going in for this process. the life of the component is sure to increase by 200% in all aspects. HVOF is also a good process but for the cost involved.
- Chennai, Kakkalur
October 14, 2010
I would look into the possibility of 0.0015" of electroless nickel. Chrome or copper nickel chrome have been a standard for a long long time.
Salt nitriding has some nice effects also. I think that Kolene has an applicable process.--Worth checking out. The information is free.
- Navarre, Florida
October 15, 2010
Q, A, or Comment on THIS thread -or- Start a NEW Thread