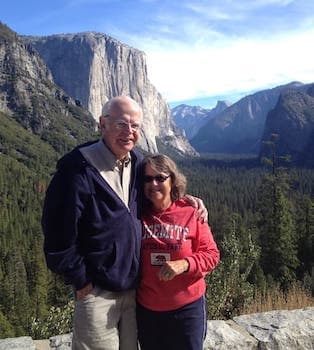
Curated with aloha by
Ted Mooney, P.E. RET
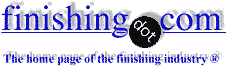
The authoritative public forum
for Metal Finishing 1989-2025
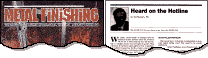
-----
Method to detect detrimental materials on surface of chromium nickel alloy tubing
June 10, 2010
Hello,
Could anyone recommend me some test to analyze surface contamination on tube made of a chromium nickel alloy. I need to assure that the following materials are below the specified value.
Chlorides plus fluorides.....100 ppm
Fluorides....................50 ppm
Sulphates plus sulfides.....100 ppm
Phosphorus...................250 ppm
If it is possible I need the standards that mention these kind of tests.
Thank you
Best regards
Engineer - Buenos Aires, Argentina
My first thought would be to swab the pieces with 18 mega-ohm di water into a clean vial. Analyze via ion chromatography.
Terry Tomt- Auburn, Washington
June 15, 2010
Dear Diego,
I don't know nothing about the dimensions of these tubes, you talk about ppm, which is defined as part per million......in a watery solution we would say milligram per liter. This description gives some discussion already, as I guess this ppm number is referring to a certain surface area on which you have to do in your measurements. Leaching this surface out in ultra pure water, followed by HPLC is the most scientific and suitable method, although I wonder if it shouldn't be ppb if the area you have to leach out is measured in square feet(s).
Another approach could be measuring the conductivity of the final rinse water to which the parts are exposed for a relatively long rinsing period and calculate this concentration back to the max. possible ionic contamination for that contaminant which has the lowest allowable level in the specification (All others will automatically be lower...rinsing time should be long enough to diffuse out fully the ionic contaminants). This could be a practical approach, which you have to discuss with your customer as well. Be aware that any manual handling of the part adds chloride to it. A lot more to tell, but a start for you, I hope. Good luck.
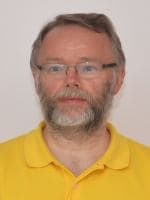
Harry van der Zanden
consultant - Tilburg, Netherlands
June 19, 2010
June 19, 2010
And regarding your question about standards:
For sure SEMI has a standard for contamination on leadframes: Nr. G52-90
This test method was technically approved by the global Assembly & Packaging Committee and is the direct responsibility of the Japanese Packaging Committee. Current edition approved by the Japanese Regional Standards Committee on July 23, 2004. Initially available at www.semi.org September 2004; to be published November
2004. Originally published in 1990.
This standard describes the procedure to determine ionic contamination on leadframes using a water extraction method. The method is sensitive to Na+, NH4+, K+, Cl−, NO3-, Br−, SO42−, PO43−.
Revision History
SEMI G52-90 (Reapproved 1104)
SEMI G52-90 (first published)
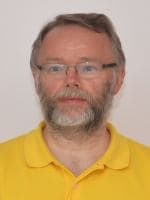
Harry van der Zanden
consultant - Tilburg, Netherlands
July 23, 2010
Dear Harry,
First of all, thanks for your response.
I have been studying your recommendation, and I think is the best way to quantify surface contamination, principally halogens. The problem is that SEMI standard do not cover elements like fluorides and is one of most important for me because, the tubes are pickled with HF.
If you know another standard that uses this method, I will appreciate it.
Thank you very much
- BsAs, Argentina
July 30, 2010
In a case like this, I would always start by asking the client what method they use to measure the contamination and/or check your results
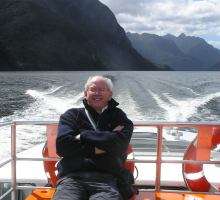
Geoff Smith
Hampshire, England
August 2, 2010
Dear Diego,
The remark of Geoff Smith is for sure a good one, but I experienced many cases in which the customer "outsourced" this to the supplier.
Sometimes you don't have a standard and in that case you need to agree on a standard with your customer. This could mean additional tests to be made to determine what the process boundaries are.
Anyway, there are several suppliers for HPLC which will guide you through the process of setting up a measuring method for F-. I'm not allowed to make commercials here, but the name of one of the good ones starts with a "D" and if you read their application note nr. 209, it will give you some idea. If I look at your limits, they really should be easily achievable. 1 mg/l. is easily detectable, but don't be upset by the equipment prices.
And another remark: if it's only for the fluoride, you can also look for a colorimeter, typical measuring range 0,1 - 2 mg/l. F-. Much cheaper!
Best regards,
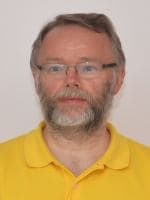
Harry van der Zanden
consultant - Tilburg, Netherlands
August 5, 2010
You may try some modern surface analysis technique like XPS ( X-ray photon spectroscopy), EDAX ( energy dispersive x-ray analysis which can be done in an electron microscope), Rutherford back scattering etc. These are all non destructive tests which quantify the contaminants on the surface. However they need small samples of about 20 mm dia.
H.R. Prabhakara - ConsultantBangalore Plasmatek - Bangalore Karnataka India
August 6, 2010
Auger spectroscopy will do all you want quickly and easily.
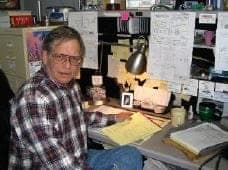
Jeffrey Holmes, CEF
Spartanburg, South Carolina
August 12, 2010
Thank you for your answers
Regarding XPS and Auger as alternatives, I need a calibrated pattern to obtain accurately measurements, and normally there are not this kind of patterns made of nickel alloys with halogens in its composition. Up to now the only possibility that I found was leaching some chips obtained by metal machining.
At first, I tried to dissolve the chips but the problem was that for dissolve this kind of alloys I need acids with halogen contents (HF, HCl) which mask the readings.
Anyway any new suggestion about this topic will be welcome.
Thank you
Diego
- Buenos Aires, Argentina
Q, A, or Comment on THIS thread -or- Start a NEW Thread