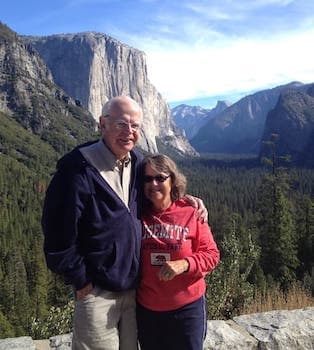
Curated with aloha by
Ted Mooney, P.E. RET
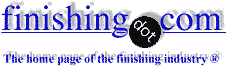
The authoritative public forum
for Metal Finishing 1989-2025
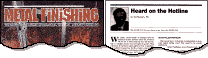
-----
Inserting self clinching fasteners in anodized parts without hardcoat cracking?
We are having an interesting problem with hard coat anodizing. When we press self clinching fasteners into the body of the part the hard coat seems to crystallize and flake off in that area. We are not the design authority and are manufacturing the part per print. Should the plating be able to withstand hardware insertion or is the specification to do so a design flaw?
Russ MacPhersonQuality Assurance Sheet Metal Industry - Londonderry, New Hampshire, USA
May 28, 2010
![]() |
Hard coat is a very good wear resistance coating, but is brittle. When you clinch the fastener, it deforms the substrate aluminum and the hard coat will flake to some extent. James Watts- Navarre, Florida Russ, Aerospace - Yeovil, Somerset, UK |
If I'm reading your post correctly, and to expand a bit on what James wrote, it sounds to me as if the actual pressing in of the fasteners is what's casing the anodizing to flake, not the function of the fasteners themselves. It almost sounds as if the hole is too small, and what you are doing is expanding the aluminum around the hole during the pressing process. If that's the case, the aluminum will give, but the anodic coating will not, as it's much harder, and as James correctly stated, much more brittle.
It's not uncommon for dowel pins to be inserted/press fit into anodized parts after coating, make sure your design specs are similar to what they'd be for a dowel pin, and also make sure that the hole is masked during the anodizing process, and you should not have problems with a good quality anodic coating.
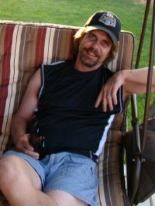
Marc Green
anodizer - Boise, Idaho
June 2, 2010
Q, A, or Comment on THIS thread -or- Start a NEW Thread