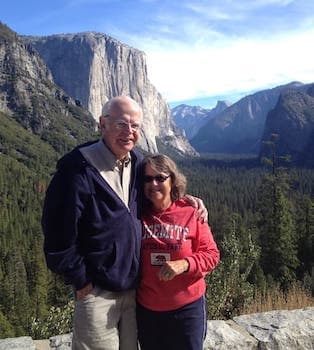
Curated with aloha by
Ted Mooney, P.E. RET
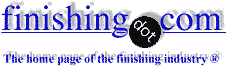
The authoritative public forum
for Metal Finishing 1989-2025
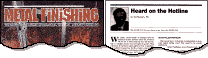
-----
Importance of sand blasting in metallising
Q. Dear Sir
We will like to know the importance of sand blasting in metallising process.We have HVAF Process and would like to know which raw material should be used for sand blasting.
Different components in various materials have to be coated and hence please advise which is the best material like sand,grit in cast iron,s.s.grit and any other suitable material.
The components to be coated include Pump Casings in Alloy Iron,S.S.Shafts,ID Fan Impellers Glass Moulds and various other items.Can river sand be used for blasting.
Thanks with regards
Yours truly
business - UP, India
May 27, 2010
A. Sand is a poor choice as it breaks down rapidly and you will spend a lot of time changing the media out. Sand typically does not have a uniform size, especially if you go the cheap route. You also do not know what impurities that it has, which will vary a bit from bag to bag. In the USA, it requires extra safety measures and record keeping because it causes silicosis.
I would choose silicon carbide as it is readily available, lasts longer than most others and is not terribly expensive. In the USA, sit requires similar paperwork as sand, but you use a lot less of it. For flame spray operations, many will choose white aluminum oxide as a compromise.
- Navarre, Florida
June 2, 2010
July 21, 2010
A. Dear Sir,
The blasting process is most essential in metallurgy work. before painting, coating, plating, winning, conning and polishing. the sand blast is very seep [cheap?] and old one, but this will pollute the air. nowadays alumina oxide is suitable for most of the metal cleaning process. Aluminum Oxide is a sharp, long-lasting abrasive sandblasting cutting media that can be re-used many times for grit blasting. As an abrasive blasting media, it is harder than most common dry abrasive blast media and will cut even the hardest metals and surfaces. This particular abrasive blasting media comes in a wide range of sizes. White Aluminum Oxide is a 99.5% ultra-pure grade of blasting media. White Aluminum Oxide is increasingly being used in critical, high performance processes such as microdermabrasion. White Aluminum Oxide is also required where contamination from other metal oxides must be kept to a minimum.
Corn Cob is a biodegradable blast media that will not etch or warp surface being blasted. Ideal for applications such as wood log homes and thin metals and plastics.
Crushed Glass Grit is a silica-free consumable abrasive that offers aggressive surface profiling and removal of a variety of coatings. Manufactured from 100% recycled bottle glass, Crushed Glass Grit produces a whiter, cleaner finish relative to mineral/slag abrasives.
Creating a softer, brighter finish than angular abrasives, Glass Beads offer a silica-free option for shot blasting, peening, honing, cleaning and light deburring. Glass Beads can be recycled up to 30 times.
Available in a variety of sizes, Urea, Acrylic, Polyester and Melamine Plastic Abrasives are ideal for applications such as auto restoration to deliver a high stripping rate without damage or warping of the substrate.
Pumice is the softest of all the blasting media yet still offers excellent stripping properties. Excellent for blasting surfaces such as soft wood to remove paint and coatings with no impact on the substrate.
Silicon Carbide is the hardest blasting media available. Silicon carbide has a very fast cutting speed and can be recycled and re-used many more times that either sand or aluminum oxide. The hardness of silicon carbide allows for much shorter blast times and lower overall cost per hour relative to other blast media.
Steel Grit is an angular carbon steel designed for quick and effective removal of surface contaminants from metals. Softer than Aluminum Oxide and less likely to fracture, Steel Grit leaves an etched surface superior for adhesion of paints and coatings.
Steel Shot is ideal for peening applications to impart a clean, smooth and polished finish. This dense, smooth shot can be used up to 3,000 times producing minimal dust during the blasting process increased compressive strength of the metal.
Walnut Shell Grit
⇦ this on
eBay or
Amazon [affil links]
is the most versatile of the organic media due to its angular, durable shape yet is still considered a soft media. Use as an economical, biodegradable alternative for sensitive blasting operations that require aggressive stripping without affect on the substrate.
- Madurai, Tamil Nadu, India
Ed. note: Very informative! Thanks, Shanmugavel.
Q. Dear Sir
Thanks for the reply with regards to grit blasting media.
We are doing twin wire spray coatings and this information is of great help.We will be using aluminium oxide grit but white aluminium grit is not available so we are using dark brownish aluminium oxide grit.Can we also use cast iron borings after sieving them through mesh size 25 or so.
Kindly advise on this.
Thanks with regards
U.P., India
July 23, 2010
Q. Sir
What is the capacity of the air compressor
[adv: air compressors on
eBay
or
Amazon [affil links] for grit blasting and at what pressure should the grit blasting be done for achieving best results.for proper adhesion of thermal spray coatings.
Thanks with regards
Gurmit Singh
- Bareilly, UP, India
July 31, 2010
Q, A, or Comment on THIS thread -or- Start a NEW Thread