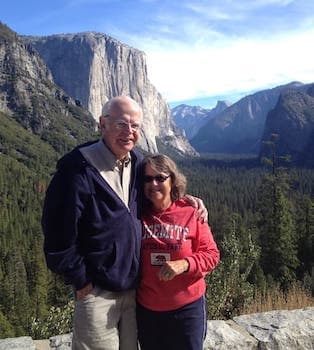
Curated with aloha by
Ted Mooney, P.E. RET
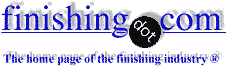
The authoritative public forum
for Metal Finishing 1989-2025
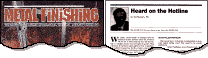
-----
MIL-DTL-5541 Type I vs. Type II (TCP) issue
Q. What's the difference between MIL-DTL-5541
[⇦ this spec on DLA] Type 1 and Type 2?
Are there any risks by changing from Type 1 to Type 2 or from Type 2 to Type 1?
- San Juan, Puerto Rico
April 15, 2021
Type 1 is hex, Type II is Tri. Your customer should specify which one.
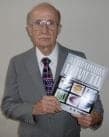
Robert H Probert
Robert H Probert Technical Services

Garner, North Carolina
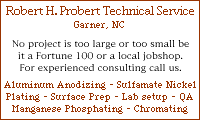
April 20, 2021
A. Hello Daniel, The biggest difference is type 1 is a hexavalent chrome which is highly regulated and gives you a yellow or gold color where type 2 is a trivalent chrome and gives you a clear or little bluish color and is NOT as hazardous as the type 1. They both have to pass the salt fog requirement in MIL-STD-5541 but the end user should be calling out which type they are looking for since some parts have a long track record with one or the other.
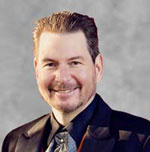
Mark Battles
Plymouth, Minnesota
April 23, 2021
⇩ Related postings, oldest first ⇩
Q. I have an aluminum housing that was chromate conversion coated per MIL-DTL-5541 [⇦ this spec on DLA] Type II... My customer is telling me that we must use Type I of this specification... I see in the spec. that Type I contains hexavalent chromium and Type II does not... Why would our customer (US military) insist upon the Type I of MIL-DTL-5541?
Bob DiamondMechanical Engineer - Hauppauge, New York, USA
May 26, 2010
A. Hi, Bob. While NAVAIR may consider the performance of Type I and Type II equivalent, the designer responsible for the component is free to not feel that way :-)
One way in which they are not equivalent is that simple visual inspection will verify the presence of a Type I coating, whereas if an area has been missed with Type II, the omission is quite likely to slip by unnoticed.
But I certainly feel you are right to try to avoid the use of toxic hex-chrome.
Regards,
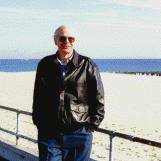
Ted Mooney, P.E.
Striving to live Aloha
finishing.com - Pine Beach, New Jersey
May 27, 2010
Q. Ted,
Thanks for your response... I understand the visual inspection issue regarding Type I versus Type II... But we use only military/space approved platers who provide fully traceable documentation, C of C's, etc. on their plating... So verifying that the chromate conversion was done should not be an issue... I am trying to understand, from a functional and corrosion protection standpoint, what the difference is (if any) between Type I and Type II...
- Hauppauge, New York, USA
May 27, 2010
A. MIL-DTL-5541F is quite specific per paragraph "3.1 Materials. If no material type is specified type I shall be used." This prevents possible unintended consequences of using a new material in applications unknown to the NAVAIR specification writers.
Chris Jurey, Past-President IHAALuke Engineering & Mfg. Co. Inc.

Wadsworth, Ohio
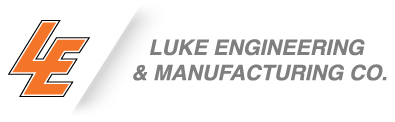
May 27, 2010
Q. I understand that the specification states that if Type I or Type II is not specified then the default is Type I (hex chrome)... What I am looking for is the actual difference in corrosion protection performance between Type I and Type II...
Bob Diamond [returning]- Hauppauge, New York, USA
June 1, 2010
A. Hi, Bob. There is supposed to be equivalent corrosion resistance -- it meets the traditional corrosion testing requirements of MIL-DTL-5541, but ...
Although I don't have field experience with substituting Type II for Type I chromate conversion coating on aluminum, I do have experience in doing it on zinc plating, and ran into a few problems including poor paint adhesion, inability to withstand a re-cleaning cycle, etc.
Just because something is generally believed to be of about equal corrosion resistance doesn't necessarily prove that it is always equivalent under all circumstances; you keep re-phrasing the question because the responders aren't 'getting it', but maybe we're resisting going in the direction you'd like :-)
For example when I say the Type II coating can be a problem because it's not visible, and you respond about "fully traceable documentation, C of C's", I still have in mind problems like trapped air pockets preventing coating on an area of the part despite any documentation.
Trivalent coatings are an important environmental advance which should be implemented when possible, and their performance may even exceed that of hexavalent coatings in some ways, but they are just not the same thing. Good luck.
Regards,
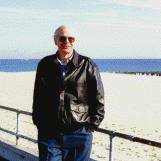
Ted Mooney, P.E.
Striving to live Aloha
finishing.com - Pine Beach, New Jersey
June 1, 2010
A. Bob
Have you considered having some coupons processed and tested to failure to give you an idea of how comparable the performance is?
- Colorado Springs, Colorado
June 1, 2010
I found several technical papers (white papers) online showing performance of the Type II trivalent chromium to be at least equal to or better than the old Type I hexavalent chromium...
After much discussion our customer has finally given us approval on the MIL-DTL-5541F, Type II conversion coating... They were never able to give us a solid reason why they insisted upon the Type I except past history (legacy).
Thanks for all of your responses on this.
- Hauppauge, New York, USA [returning]
June 4, 2010
Q. I am also trying to prove the equivalence of MIL-DTL-5541 Type II conversion coating to Type I in terms of corrosion resistant performance.
Could you please refer me to the technical papers that support this?
I have been searching technical papers from the Army Research Laboratory and NASA publications on this topic but some papers are outdated or don't show direct comparisons between the two types.
Thank you.
- Goleta, California, USA
May 18, 2011
Junior Sales Representative - Resintech, Camden, NJ
Nadcap Chemical Processing Auditor - PRI, traveling
Process Engineer / Chemist - Denver Metal Finishing, Colorado
Q, A, or Comment on THIS thread -or- Start a NEW Thread