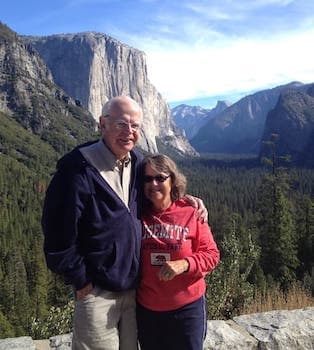
Curated with aloha by
Ted Mooney, P.E. RET
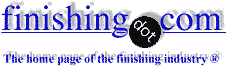
The authoritative public forum
for Metal Finishing 1989-2025
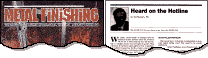
-----
Effects of MIL-DTL-5541, Type2, Class1A on Pressed In Captive Hardware
Hello all, we are a electronic design/CM house serving various industries from medical to automotive. One of the projects we are currently in alpha development on will be used in a marine environment with ROHS compliance.
The external panels of the part are aluminum sheet metal with various PEM captive hardware pieces pressed in. To minimize part handling, we have specified the PEM hardware be pressed in prior to finishing, and called out Chemical Film per MIL-DTL-5541, Type 2, Class 1A to be applied to the entire part. The PEM items in question are RAS-832-9-Z1 (sintered Distalloy 4700 w/Zinc Plate per ASTM B633, SC1, 5um, Type 3, colorless).
When the parts came back from the plater, the PEM inserts had changed color to a dark olive green. I suspect part of the Chemical Film process caused this change, but I'm ignorant as to what part of the process may have caused it.
The question is: Is there any corrosion protection on the dark olive green PEM parts after Chemical Film?
An obvious alternate path would be to install the PEM hardware post-plating, which we will specify if there is no other alternate.
Thanks!
Product Designer - Gray, Maine, U.S.A.
May 12, 2010
1. MIL-DTL-5541, Type 2, Class 1A is non-hexavalent while ASTM B633 Type 3 is hexavalent. Perhaps you wanted to specify Type 6 to maintain RoHS? It seems a lot of people disregard the last 2 additional types allotted in the spec.
2. SC1 is a fairly light Zn application for such an application (marine). I'd be concerned of premature corrosion. Would Pems RAA fit the bill? It would eliminate this issue all together.
3. I'm curious if the chromate process for the aluminum (5541) has damaged or enhanced the chromate for the Zn (633). I'd trust a salt spray test on a finished part over the guess of a finisher. Ken Jacques
- Meriden, Connecticut, USA
August 17, 2010
Hi Chris I have some comments, but I'm not entirely sure they'll answer your questions.
Thanks for the reply.
Our customer has decided to powder coat the items in question, so this issue is no longer active.
In regards to the RAA insert, they are only available non-threaded (for self tapping/rolling screws). We did not want to risk the introduction of loose metal fragments during assembly (possible floating shorts in an electronic assembly).
- Gray, Maine, U.S.A.
August 27, 2010
Q, A, or Comment on THIS thread -or- Start a NEW Thread