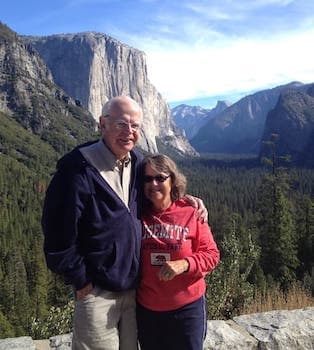
Curated with aloha by
Ted Mooney, P.E. RET
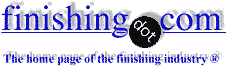
The authoritative public forum
for Metal Finishing 1989-2025
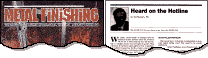
Thread 549/71
Bubbles and Blister formation during trimetal plating
May 5, 2010
Dears,
We are manufacturing bronze bearings. these bearings go through many process before plating. Plating operations include nickel barrier plating to avoid the migration of tin, after this it is plated with tri metal plating using flouboric salts of lead tin and copper. After entire processing the plated surface shows formation of blister and bubbles. kindly suggest suitable action to avoid the such occurrences.
regards
- India
publicly reply to Sandeep Saykhindikar
May 5, 2010
Hi, Sandeep. You need to remove the blisters and look at the substrate and the underside of the blisters to determine whether the nickel is not adhering to the bronze, or the trimetal is not adhering to the nickel. In the former case, you need to examine the cleanliness of the bronze and that your pretreatment acid is appropriate. In the latter case you need to either proceed immediately from nickel plating to trimetal plating, or you need to activate the nickel surface with a nickel strike. Good luck.
Regards,
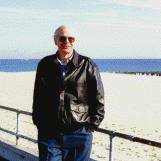
Ted Mooney, P.E.
Striving to live Aloha
finishing.com - Pine Beach, New Jersey
publicly reply to Ted Mooney
May 11, 2010
Dear sir,
It is observed that Trimetal is not adhering to the Nickel barrier plating, you suggested that trimetal plating should be immediately followed after nickel plating, as per our process after nickel plating, there are two tanks for the nickel solution drag out and rinsing , after that it is dip into an activation bath consist of Hydro fluoboric acid for some time & then it is proceeded to tri metal plating, so do I need to change which is 3 minutes after nickel plating kindly suggest.
Regards
- India
publicly reply to Sandeep Saykhindikar
June 3, 2010
Dear Sandeep,
Following are the solutions for your problem of blisters
1. As you said the peeling after Nickel, then alloy plating adhesion is poor. Check for the pH of the Nickel bath and maintain between 2.8 to 3.2
2. Check for any power failure. Because as the alloy contains copper, electrical connection should be established as the component goes in. Switch on the rectifier as the rack goes in.
3. Adopt post plate baking at 160 °C to overcome this problem.
4. Check the copper content in the plating bath and maintain in between 2 and 2.5 g/l max.
hope this will solve your problem
All the best.
- Bangalore, Karnataka
publicly reply to SHANKARANARAYANAN NARAYANASWAMY
Q, A, or Comment on THIS thread -or- Start a NEW Thread