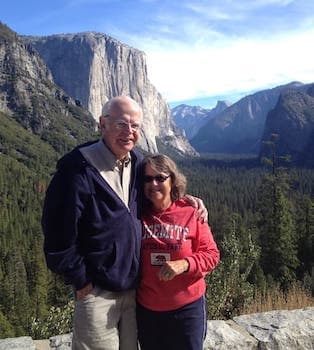
Curated with aloha by
Ted Mooney, P.E. RET
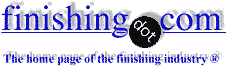
The authoritative public forum
for Metal Finishing 1989-2025
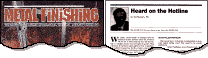
-----
Difference between copper anodes with phosphorous content
April 29, 2010
Hi. I work for a plating shop where we plate hard copper on MS based cylinders to be used for electromechanical engraving. We use following electrolyte composition.
CuSO4: 200 to 230 gm/ltr.
H2SO4: 60 to 65 gm/ltr.
Chlorides: 2-4 ppm max.
Bath temperature: 28C
I have two questions which are listed below and would appreciate a reply for which I thank you in advance.
1. Normally we are able to achieve hardness of the plated copper around 185 to 195HV and would very much like to hit 200 to 210 HV. If I try to pump more hardener in, the Ballard shows brittleness. I have tried reducing the hardener dosing thinking maybe it is being over dosed but still no result. How can I get the desired and consistent hardness of plated copper?
2. What is the difference in using phosphorized anodes and non phosphorized anodes, meaning what effect does its presence or absence have on plating result or the process?
Once again I thank you in advance for your replies.
Wish you a nice day.
Employee - Gujranwala, Punjab - Pakistan
Hi Raza,
phosphor content for copper electrolytes in rotogravure should not exceed 0.04-0.08% of phosphorous. If you are using non-phosphorous it will effect the ability of dissolving the anodes.
About your problem, depends which additive you are using, the content of chlorine is too high. Some additives in the rotogravure work without any chloride to provide ductility which is necessary for a good engravable copper.
Try to increase your bath temperature to 30 degrees.
Best regards,
- Melbourne, Australia
April 30, 2010
May 6, 2010
Dear Dominik,
Thank you for your valuable reply.
The OFHC grade anode we use contains Phosphor 3 ppm max. Do you think its presence can produce sludge?
We tried another brand of hardener additive which required chlorides level in the range of 100 to 150 ppm? With this additive not only the surface of plated copper was shinier but the hardness was always within 205 to 215HV range having good ductility as well.
Before making a switch we wanted to know why we had problems with the existing additive plus we have an ample amount of it in stock which needs to be consumed first.
Increase in bath temperature failed to bring up the hardness as it stayed in the same range as was before the increase 185 to 195 HV.
Once again I would like to thank you and would appreciate any further suggestions from you or anyone else.
Wish you all a nice day.
- Gujranwala, Punjab, Pakistan
adv.: Supplier of Copper Anodes, Nickel Anodes, Bismuth Metal, & Other Metal Products for Industry & The Arts
Q, A, or Comment on THIS thread -or- Start a NEW Thread