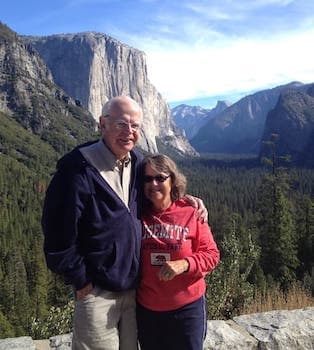
Curated with aloha by
Ted Mooney, P.E. RET
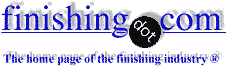
The authoritative public forum
for Metal Finishing 1989-2025
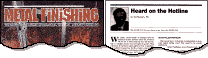
-----
Why is Hot Dip Galvanized coating thickness dropping?
April 27, 2010
Hi Everyone,
I have been reading through these forums for some time now and the information is amazing, I am working in a hot-dip galv plant and am still learning a lot. However I have come across a problem which I first thought was a badly calibrated elcometer. The zinc coating on our products has gradually become quite thin (over a wide variety of steel, types and sources) and I am unsure where to look to rectify the problem.
I have read that you can purposefully make a flux to lower the amount of extra zinc deposited on the steel but I can't figure out where our problem would be coming from. We used to have the situation of a thick coating well above the standards and this had never been a problem, but we haven't changed anything that I know of.
Cheers,
HDG Plant Manager - New Zealand
April 30, 2010
Most galvanizers want to reduce the thickness as they "give away" more zinc than the standard calls for.
There are many factors affecting coating thickness.
Steel chemistry (especially Silicon and phosphorous)
Immersion time
zinc temperature
flux chemistry
Nickel content.
What's your setup in this respect?
I wonder if being in the southern hemisphere has any effect? Does all the zinc go on the underside?
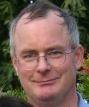
Geoff Crowley
Crithwood Ltd.
Westfield, Scotland, UK
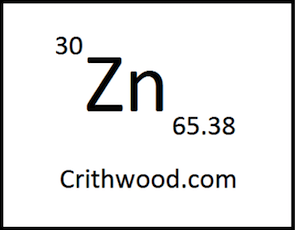
May 4, 2010
Sir:
I have been told that 85% to 90% of the steel in Australia is relatively non-reactive (giving thin zinc coatings), perhaps your steel is similar. Adjusting the coating thickness to thicker zinc is done by higher zinc temperature and longer kettle times.
My two articles: "MAGNETIC THICKNESS GAUGES AND STANDARDS PART 1," Metal Finishing, March 1994; and MAGNETIC THICKNESS GAUGES AND STANDARDS PART 2," Metal Finishing, April 1994, would help you. Several hundred thousand readings were made over three years for these articles. They can be obtained via interlibrary loan as xeroxed copies.
The top gauges that best measured hot dip galvanized coating thicknesses were "banana," permanent magnetic, single point calibration, "pull off," type and gave the highest precision and accuracy. Standard coatings must be attached to the steel for this type of gauge. The top gauges are made in the USA and Germany.
I have no comment regarding double point calibration, electronic Elcometers.
Regards,
Galvanizing Consultant - Hot Springs, South Dakota, USA

Q, A, or Comment on THIS thread -or- Start a NEW Thread