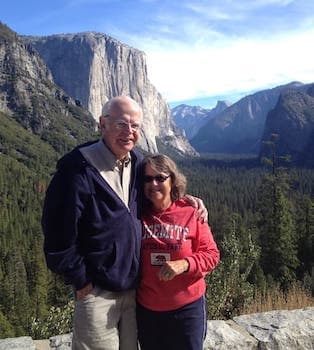
Curated with aloha by
Ted Mooney, P.E. RET
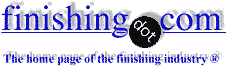
The authoritative public forum
for Metal Finishing 1989-2025
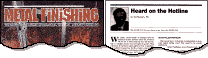
-----
Best marine finish for cast A380 part
April 20, 2010
I have a nice cast part made in China, but every finish they try only lasts about 4 weeks. I requested a "stove enamel" like used on cast marine cleats I have experience with (Clamcleet®), but I am not getting anything like it.
I want a finish like a cast auto wheel which seems to last decades in salt and weather.
designer - Hawaii
May 2, 2010
Need to update a few things here. The part is A360 , not A380.
I am very interested in Hard Anodizing this part.
Good Idea, Bad Idea? Is it even possible?
Thanks, Jeff
designer - Kahului, Hawaii, USA
Neither of these alloys, A360 or A380, are good candidates for anodizing in general, and hard anodizing in specific. They are high silicon content alloys, which optimizes the metal fluidity during the high pressure die casting process, but it hinders the development of a proper oxide layer during anodizing.
Castings need very good preparation for painting, including removal of the die lubricant on the surface. Porosity is another concern. Regarding coating selection, typical automotive wheels use a primer + basecoat + clearcoat process. Primers are usually polyester powders, while basecoats can be either acrylic (liquid) or polyester (powder). The final clearcoat can be either acrylic (liquid or powder) or polyester (powder). Total thickness is on the order of 100-200 micrometers.
Automotive components supplier - Michigan, USA
May 5, 2010
Luke Engineering and Manufacturing Co Inc has developed a special process, LUKON DC, for forming hard anodic coatings on aluminum die-castings. Hardcoat as thick as 2 mils (50um) is possible. Luke hardcoats more than three million of these die-castings per year. Like most anodic coatings, this is also an excellent base for further topcoatings such as paint or powdercoat.
Chris Jurey, Past-President IHAALuke Engineering & Mfg. Co. Inc.

Wadsworth, Ohio
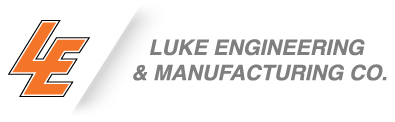
May 7, 2010
Q, A, or Comment on THIS thread -or- Start a NEW Thread