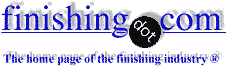
-----
Deburring machined brass and copper parts
I work for a screw machine company and we recently inherited some work from another shop that went out of business. Several of their part families were produced with burrs and then dipped in acid to remove those burrs. Unfortunately, we have never done acid deburring and did not receive any process information when the jobs transferred so are starting from scratch to develop a capable and repeatable process. I read about bright dip formulas on this site and have been using a solution of 50 ml 65% nitric acid mixed with 350 ml 75% phosphoric acid. We are conducting the etch in a glass beaker [beakers on eBay or Amazon [affil links] contained inside a small fume hood that is rated for acid. This works reasonably well on small batches but I have noticed that acid straight out of the refrigerator (where it is stored) cuts much more slowly than acid at room temperature so it's obvious that temperature plays an important role in the process and must be controlled. We are going to be making larger volumes and I have to be able to take this out of R&D and turn it over to a trained operator but I am somewhat in the dark with regard to bath process temperature control, monitoring and pH replenishment. Therefore, I am looking for any type of literature or guidelines on how to start and maintain a small acid process bath to perform deburring operations.
Hollis WooldridgeDirector of Quality - San Antonio, Texas, USA
April 15, 2010
April 19, 2010
For many, but not all, reactions, a 20 degree F rise in temperature will double the rate of reaction (for a while).
The chemistry has to remain fairly close on the reactant side and some of the products must precipitate out to keep up this rate.
I do not know, but I suspect that it is the nitric that dissipates faster than the phosphoric, so you need to do regular analyses to determine the additions. If the products do not precipitate to a fair degree, then a dump or a bleed & feed operation will be required.
- Navarre, Florida
Q, A, or Comment on THIS thread -or- Start a NEW Thread