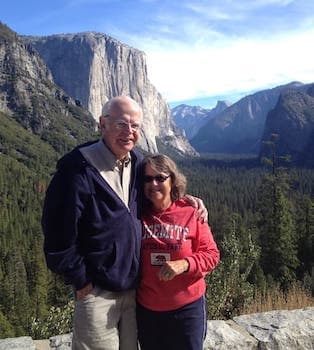
Curated with aloha by
Ted Mooney, P.E. RET
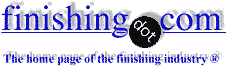
The authoritative public forum
for Metal Finishing 1989-2025
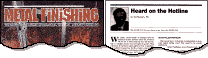
-----
Electro galvanized coating thickness
Q. Kindly let me know the min. & max. coating thickness possible in the Electro galvanizing process for small springs & spring washers.
Rajesh Raj- Kozhikode, Kerala, India
April 5, 2010
A. Hi, Rajesh. There is no minimum thickness, although there is probably a minimum beneficial thickness in the neighborhood of .0001". The maximum practical thickness is probably somewhere around .0006 to .0008". You might want to consider mechanical galvanizing or hot-dip galvanizing above that thickness. In fact, due to hydrogen embrittlement issues, you may want to consider mechanical plating in any event. But please describe your situation rather than posing your inquiry in abstract fashion, because hypothetical questions can never be properly answered without a hundred ifs, ands, and buts. Thanks.
Regards,
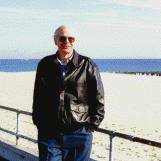
Ted Mooney, P.E.
Striving to live Aloha
finishing.com - Pine Beach, New Jersey
Q. What is the difference in corrosion protection between 3-5 micron electro galvanized coating and 5-12 micron electro galvanized coating?
Mike Sharpless- Union City, Georgia
April 19, 2013
A. Hi Mike. 5-12 microns will give roughly twice the corrosion protection of 3-5 microns.
Regards,
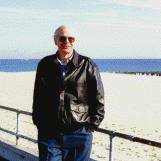
Ted Mooney, P.E.
Striving to live Aloha
finishing.com - Pine Beach, New Jersey
April 22, 2013
Q. Thanks for answering my initial question about the difference between 3-5 micron and 5-12 micron coatings. I figured it would be about twice as much. Now, I would like to know what is the protection rating for 3-5 micron? Is it measured in a salt spray test?
Mike Sharpless- Union City, Georgia
April 23, 2013
A. Hi Mike. I know that this kind of answer isn't very satisfying, but the question itself is fraught with ambiguities for lots of reasons. First, salt spray testing is a QA assurance mechanism, not a predictor of real life. Second, salt spray testing of zinc coatings is misleading 100% of the time because it doesn't allow the zinc carbonate corosion products to form that offer the actual long term protection to zinc coated products. Third, the salt spray performance is as dependent (if not more so) on the chromate conversion coating and topcoat than on the zinc plating. I think the best answer is that a 4 micron zinc coating is only for "mild" corrosion conditions (indoors) whereas 10-12 microns might offer "moderate" corrosion protection, such as for underhood automotive components. You could probably request a coating suitable for 96, 128, or 192 hours of salt spray, and you'd probably see inconsistent results with 3 microns, but good results with 8 microns or more.
Regards,
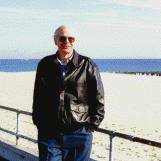
Ted Mooney, P.E.
Striving to live Aloha
finishing.com - Pine Beach, New Jersey
April 23, 2013
Q, A, or Comment on THIS thread -or- Start a NEW Thread