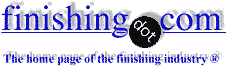
-----
Appropriate micron level for anodizing
March 31, 2010
Hi there,
We're a commercial office partitioning systems provider, with our own designs that we send to manufacturers to extrude and then anodize. The billet that the manufacturer uses, complies to 6063T5 standard. The manufacturer has seriously invested in, and utilizes recycled technology as part of the billet manufacturing process.
Recently, we have introduced a hairline stainless steel anodized finish to our office partitions. We have been told that in order to get a shiny appearance, the level of microns that the product will be anodized will drop down to 2-3 microns. [We previously used a 12 - 15 micron finish for standard anodizing].
My question is:
a) Is 2-3 micron coverage good enough for a commercial office interior environment?
b) Are they correct in advising us that they drop their micron levels? and
c) Is 6063T5 appropriate for what we are trying to achieve? Our product is not structural, but does need quite a bit of strength to hold doors, withstand door slams, impact resistance etc. Typical heights are up to 3 m high.
Many thanks in advance.
Product designer - Bangkok, Thailand
Hi, Suresh. I'm not sure if you are confused or I am. But I'm not sure what you mean by "appropriate micron level". If you are saying that the anodizing thickness used to be 12 - 15 microns, this is quite heavy but certainly not unheard of for standard anodizing. But 2 -3 microns is very thin; I don't think it's enough and I don't understand your overall situation. Good luck.
Regards,
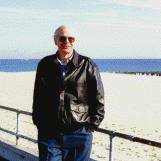
Ted Mooney, P.E.
Striving to live Aloha
finishing.com - Pine Beach, New Jersey
April 1, 2010
Hi Suresh,
While 2-3 microns of anodizing is sufficient enough for light reflectors and such, it will be inadequate for architectural surfaces. generally such thin coatings are not even sealed to preserve the luster. Architectural anodizing has to be sealed to preserve the properties of the anodizing film.
Anodizing as you know is mainly for surface protection of aluminum and for aesthetics. The humid weather in our countries can affect the underlying aluminum in the long run. Also the thinner coatings will be more prone to scratches while cleaning or dusting and would further lead to deterioration. Damage to the surface could also occur while assembling the structures.
If the final finish you require dictates a really thin anodized coating, you should consider going in for clear lacquering after the anodizing. This would lead to increase in cost but should serve as additional protection for the aluminum.
I hope this helps.
- Bombay, India
April 3, 2010
April 5, 2010
Suresh
a] As mentioned, 2-3 micron is probably inadequate for your application. 10-15 should be.
b] It is quite possible that your material will start loosing its' shine or brilliance when anodized to 10-15 micron thickness. By thinning the anodize, a brighter finish can be obtained at the sacrifice of wear resistance. By trying to produce a 'hairline stainless steel' anodize, they may need to thin the coating. Perhaps your finisher can not play with process parameters to achieve your desired finish. Have you received samples from them at different thicknesses to compare the effect thickness has on appearance? Perhaps a bright dip is in order.
c] I am not qualified to tell you the suitability of your material for a particular application where structural integrity is a concern.
- Colorado Springs, Colorado
Q, A, or Comment on THIS thread -or- Start a NEW Thread