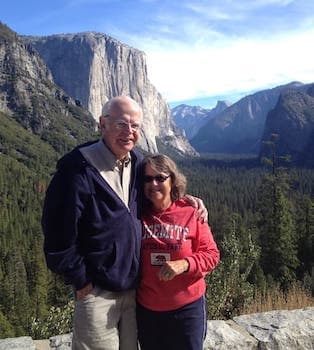
Curated with aloha by
Ted Mooney, P.E. RET
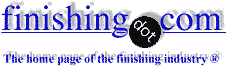
The authoritative public forum
for Metal Finishing 1989-2025
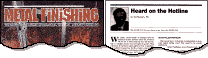
Thread 546/46
How to avoid flow marks in electropolishing process
Q. We are facing defect such as flow marks (lines) at the hole area on the SS Electropolished components. request you to kindly advise.
Rajesh ThakarkarIndustrialist - Goa, India
March 24, 2010
publicly reply to Rajesh Thakarkar
First of two simultaneous responses --
A. You may rotate the part in the process
Ricardo BursteinBnei Berak, Israel
March 27, 2010
publicly reply to Ricardo Burstein
Second of two simultaneous responses --
A. Rajesh,
Flow marks are caused by gas flowing over the surface of the component producing increased agitation and consequently a higher rate of dissolution compared with surrounding areas. Ways to prevent/minimize the effect are:
Try to ensure that critical surfaces are facing upwards so that the gas rises vertically rather than flowing over the component. This ,of course, will result in the other side being downwards facing and more affected.
Use agitation to disrupt the gas flow. Mechanical movement is usually better than air agitation. Vertical agitation is usually more effective than horizontal movement (and more difficult to achieve!)
Keep processing time to a minimum so that the marks are less pronounced.
If the additional costs can be borne, re-rack the components at intervals to move the flow line around.
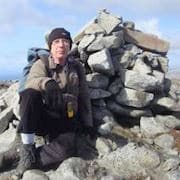
Harry Parkes
- Birmingham, UK
March 27, 2010
publicly reply to Harry Parkes
A. Re-positioning while re-racking with small intervals will eliminate the problem.
Sachin Kanse- Belgaum, Karnataka, India
May 12, 2010
publicly reply to Sachin Kanse
Q. I work for a plastic plating company and recently face flow mark issue. The part is a small square button with flow mark at the gating area.
This flow mark is only detected after the plating process is complete. Should I follow the same countermeasure in this thread?
Or do you have any countermeasure for plastic parts which face this flow mark issue?
The idea of keeping process time at minimum side attracts me to give it a try.
Please advise and thank you in advance.
employee of plating company - Malaysia
July 10, 2012
publicly reply to Norddin
Q, A, or Comment on THIS thread -or- Start a NEW Thread