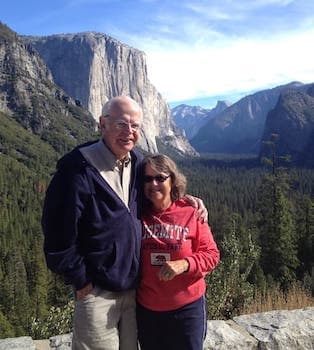
Curated with aloha by
Ted Mooney, P.E. RET
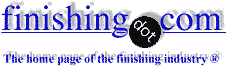
The authoritative public forum
for Metal Finishing 1989-2025
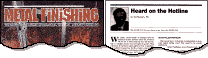
-----
Controlling fumes from hot dip sheet galvanizing kettle
March 22, 2010
We are in the galvanizing industry for the last forty years and our bath for galvanizing sheet constitute the following.
1. Kettle; made out of AG steel of thickness 32 mm and measuring 2400 L x 1600 W x 1100 H.
2. Molten lead; 32 MT
3. Flux box; Containing molten ammonium chloride floating on lead.
4. Zinc box; containing molten zinc 4 MT floating on lead.
5. Guider; made out of mild steel mounted on the kettle to guide the sheets.
6. Pair of flux rollers; to drive the sheets in to the bath for galvanizing.
7. Pair of finish rollers; to drive the zinc coated sheets out.
8. Magnetic rollers; to deliver the sheets.
9. Sprayer; to spray ammonium chloride powder by an air blower on zinc coating to provide an inert atmosphere preventing oxidation.
Galvanizing bath is enclosed in a furnace heated by heavy duty oil burners to a maximum of 950 °C.
Emission from galvanizing consists of white ammonium chloride fumes which is extracted by a 20 HP motored fan and sent out to air through a 45 feet tall stack.
Our main problem is to control the emission to a minimum level and to avoid air pollution which is mainly due to the ammonium chloride powder. The bath temperature is maintained at 450 - 460 °C.
How can we minimize the air pollution? Is there any alternative to the existing method?
The zinc we use is 99.995% pure.
Your early reply will be very much appreciated.
Best Regards.
Factory Manager - Ratmalana,Wetern Province, Sri Lanka

Q, A, or Comment on THIS thread -or- Start a NEW Thread