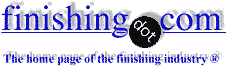
-----
Iron contamination of austenitic stainless steels results in rust and further corrosion
I work in the food processing industry and we have issues of iron contamination of austenitic stainless steels on occasion. This contamination results in rust on the surface of the stainless steel which if not arrested seems to continue indefinitely. I understand the mechanisms for possible contamination. What I need is an understanding of why the stainless steel will not create a passive chromium oxide layer after being exposed to this contamination. Can any one Please explain the mechanism responsible for this, and what can be done to correct the problem. It would be most convenient to be able to correct the problem when parts are in place.
Tim VaughanProject Engineer - Pueblo, Colorado, USA
March 18, 2010
First of two simultaneous responses -- March 23, 2010
Tim
Passivation is achieved by removing free iron from the surface and forming / promoting a chromium rich oxide film. If not passivated, free iron present on the surface will rust. Free iron can be from surface contamination or from the material itself- think pancake batter that is not fully mixed and the pockets of unmixed batter is iron that may be at the surface. You can remove the rust and still have the iron present-chemicals that passivate do not necessarily remove rust, and vice versa. As long as the free iron is present, it can rust. To correct the problem, you would have to remove the rust and iron to be able to form the passive layer
On site cleaning and passivating can be done although I have no experience with it.
- Colorado Springs, Colorado
Second of two simultaneous responses -- March 24, 2010
Dear Tim,
On occasion, rust is noticed on new stainless steel after delivery from a fabricator.
This is most often the result of embedded Fe in the stainless. When exposed to a moist or humid atmosphere, the iron corrodes leavening rust on the stainless steel surface. These embedded particles can initiate crevice corrosion. (From this I conclude that the Fe-particle itself starts the rusting-process , I don't know if I talk nonsense, but I can imagine myself that the presence of the anodic Fe particle initiates a potential difference in the direct surrounding, which reduces the oxide layer -on which the corrosion resistance properties of SS are based-of the SS and thereby initiates new corrosion to the SS surface itself.)
You primary target should be to agree on proper specifications with your vendor.
Good practice is to avoid machining and storage of SS in rooms where also steel parts are treated, in short, look for a vendor who's not machining both steels on the same machinery or thoroughly cleans the machines and takes all precautions to prevent this contamination.
(Cases are known of people using steel brushes afterwards on the SS with devastating effects).
The embedded Fe can be removed by Pickling. The normal procedure is a nitric/hydrofluoric acid bath at 120°F. (Keep in mind that working with fluorides is a real pain in the ass, dangerous and environmental unfriendly....so know what you do before you even start!.....outsourcing to a knowledgeable company is what I advise you).
The pickling solution removes a surface layer sever microns by corrosion, leaving the pickled surface in its most corrosion resistant condition. Low carbon or stabilised grades of stainless are best suited for this operation because the process may cause intergranular corrosion in heat affected zones of unstabilised grades of stainless. This procedure will also remove heat tint
Other possibility is electropolishing, however it the shape of your part is more complicated, this becomes more difficult too.
Have a look at this site (of the british stainless steel association) too:
http://www.bssa.org.uk/topics.php?article=55
Success,
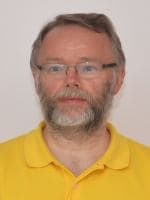
Harry van der Zanden
consultant - Tilburg, Netherlands
March 25, 2010
Tim,
As the two gentlemen before me said, taking care of iron contamination (or preferably avoiding it) is very important.
The chrome oxide layer that stainless steel has is still vulnerable under bad conditions, such as embedded bits of carbon steel that start rusting and then spread the corrosion to what's underneath the passive layer of the surrounding stainless.
Let us know if we can help.
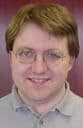
Ray Kremer
Stellar Solutions, Inc.

McHenry, Illinois
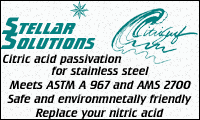
Q, A, or Comment on THIS thread -or- Start a NEW Thread