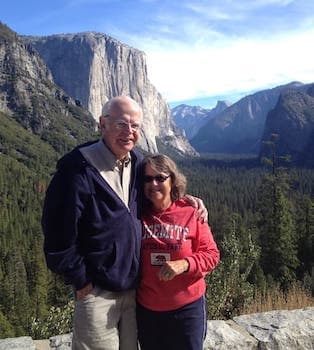
Curated with aloha by
Ted Mooney, P.E. RET
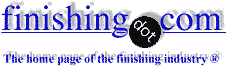
The authoritative public forum
for Metal Finishing 1989-2025
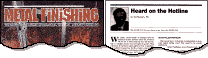
-----
Solderable Plating on Beryllium Copper to Survive Heat Treat
March 18, 2010
I am a mechanical engineer at an electronics company. I am working on a custom battery contact for a motion sensor. The contact is custom due to the sensor's extremely low current draw.
The contact spring is formed from beryllium copper in a progressive die with a cold-headed fine silver / copper contact swaged into it. After forming, it undergoes heat treatment at 600-625 F for 1-1.5 hours.
I am looking for a process that will allow me to keep Beryllium Copper solderable after heat treat.
Due to the fine silver contact face, we cannot use standard electroplating with copper strikes as this would cover the silver. Currently we are using immersion silver to plate the clip after forming. Because it is a substitutive process, it only plates the copper section of the parts. However, because it is not a standard metal finishing process, used mostly on printed circuit boards, it is difficult to find shops that provide it and there is little knowledge about plating formed parts with it. We are currently having some issues with incomplete plating.
Other than prohibitively expensive gold, palladium, etc. plating, is there any plating that could survive the forming and heat treat process? Is there any other post-plating process that would not compromise the fine silver contact face?
Any help is greatly appreciated.
Thanks,
Product Designer - Coopersburg, Pennsylvania, USA
First of two simultaneous responses --
As I understand after the heat treatment you have a black copper beryllium.So you have to options:to avoid the oxidation by heating in vacuum or cleaning the oxide by chemical special treatments and maybe silver plate the all part after this.
Ricardo BursteinBnei Berak, Israel
March 20, 2010
Second of two simultaneous responses --
Look at low-phos electroless nickel. Circuit board shops usually have that process. It will need a good activation step after heat treat to get rid of the passive film that forms, but it does solder well once you get a good process set up for your part.
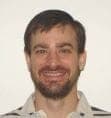
Jon Barrows, MSF, EHSSC
Independence, Missouri
March 22, 2010
First of two simultaneous responses --
Thank you for your responses. In both cases, I am worried about the silver contact face on the bimetallic part we swage into the copper spring.
Could the chemical treatment / activation possibly damage the fine silver face on our contact?
Mr. Burstein:
I am considering a silver plate without copper strike to keep from covering the nice silver contact with copper, which has higher contact resistance. Would a straight silver plate adhere properly to the BeCu?
Mr. Barrows:
Would the electroless nickel cover both the spring and the silver contact face?
- Coopersburg, Pennsylvania, USA
March 22, 2010
Second of two simultaneous responses --
Maybe you don't need a vacuum furnace, just one that has a controlled atmosphere. G. Marrufo-Mexico
Guillermo MarrufoMonterrey, NL, Mexico
March 22, 2010
After reading your post more carefully, I think that Mr. Burstein's response is better. Either control the atmosphere in the oven to avoid the oxidation or silver plate.
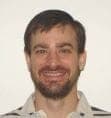
Jon Barrows, MSF, EHSSC
Independence, Missouri
March 23, 2010
Q, A, or Comment on THIS thread -or- Start a NEW Thread