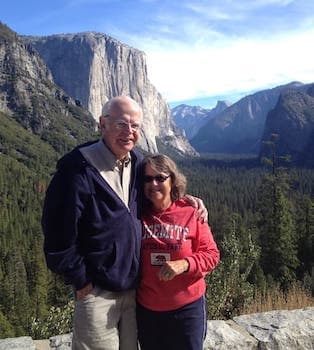
Curated with aloha by
Ted Mooney, P.E. RET
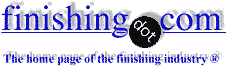
The authoritative public forum
for Metal Finishing 1989-2025
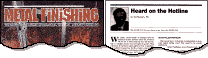
-----
Hard Anodize Problem on AL2024
Q. We are struggling with hard anodizing (MIL-A-8625 type III) on AL2024. The spec says that the thickness should be 0.002", but we can only achieve 0.001" after anodizing for 6 hrs, and we found out that longer time will not give us the thicker film. Here are our processing tank parameters.
- Sulfuric Acid Concentration: 25%
- Voltage: 20 V
- Tank Temp: 0 to -2 degree C
- Time: 6 hrs to achieve 0.0010" (25 micron). From our experiment, more time will not result in thicker film.
Can anyone suggest what we did wrong? Thank you so much in advance for your help.
Special Process Manager - Bangkok, Thailand
March 9, 2010
![]() |
A. Your acid is significantly too high, especially if it is % by volume using 64 degree sulfuric. - Navarre, Florida March 11, 2010 A. Do you understand that half the thickness is on top of the original surface and half is under the original surface ± 10%, therefore if you measure 0.001 on top, you must already have "0.002". Or does the customer want 0.004? ![]() Robert H Probert Robert H Probert Technical Services ![]() Garner, North Carolina ![]() March 11, 2010 |
A. The acid concentration can be run that high, it's just not very common. It has the advantage of being more conductive and the disadvantage of being much less tolerant to dissolved aluminum. I do agree with James that your final voltage is very likely too low. You need to continue your ramp to achieve the current density and ultimately the thickness that you need.
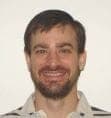
Jon Barrows, MSF, EHSSC
Independence, Missouri
March 13, 2010
A. Also agree with James that your voltage appears to be far too low. I have always controlled the process by current density, which can have quite high voltage requirements.
The concentration isn't a problem, I have used solutions of this strength before, but you do need to drop the temperature if you are using this concentration, -5C to -10C will work best, but keep the temperature below -3C.
Aerospace - Yeovil, Somerset, UK
March 17, 2010
February 26, 2019
Treatment &
Finishing of
Aluminium and
Its Alloys"
by Wernick, Pinner
& Sheasby
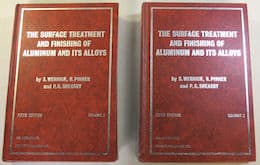
(note: this book is two volumes)
on eBay or
AbeBooks
or Amazon
(affil links)
Q. We are working towards our NADCAP accreditation but are struggling with completing the Hard Anodize process on the 2024 AL test panels. They keep burning during the process. I would appreciate any advice on how to produce a good TYPE III coating on the 2024 test panels. Here is what we have tried:
Racking Method: Aluminum (6061) Claw Clips
Tank Temp: 28-32 degrees
Sulfuric Concentration: 220-245 g/L
18v X surface area (sq/ft) - 5 min
20v X surface area (sq/ft) - 5 min
22v X surface area (sq/ft) - 5 min
24v X surface area (sq/ft) - 40 min
I am considering the 40V process mentioned above but am not sure what the ramp up process should be for that.
Thanks.
Anodizing - Spokane, Washington
A. Figure the area of the part and plan for 24 amps per square foot. Be sure the rack "tips" are wide enough to deliver that much current. Put the part in the tank at zero voltage. Spend 15 minutes slowly, evenly, raising the voltage until you get to the "target" amperage (again, try to get to the target amperage at 15 minutes. not before).on the ammeter. Now switch over to current control, tell the rectifier to HOLD the target amperage and let the voltage automatically climb to overcome the resistance of the building thickness. You will only get about 0.001 hard enough with 40 volts, you need 60 volts to get 0.002.
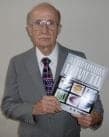
Robert H Probert
Robert H Probert Technical Services

Garner, North Carolina
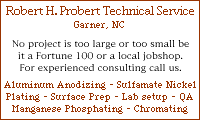
February 27, 2019
To minimize "burning" potential on any hardcoat:
1) Use the thickest panels allowed by specification. More mass helps dissipate heat, thin sections have a tendency to burn.
2) Round off all sharp edges and corners. Excess power is focused on these points, i.e., lightning rod effect.
3) Bolt the panels in a thru hole using aluminum nuts. This insures firm, full contact.
Luke Engineering & Mfg. Co. Inc.

Wadsworth, Ohio
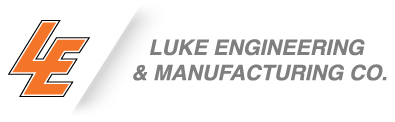
February 28, 2019
Q, A, or Comment on THIS thread -or- Start a NEW Thread