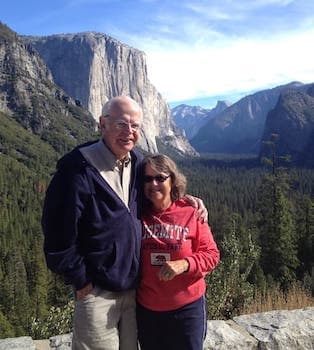
Curated with aloha by
Ted Mooney, P.E. RET
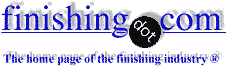
The authoritative public forum
for Metal Finishing 1989-2025
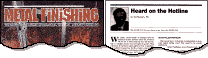
-----
Thickness of Galvanizing on MS Section
Please guide me how much thickness of zinc is required in hot dipped process for MS Section for good result.
Dinesh Rai- Delhi, India
March 7, 2010
Hi, Dinesh. In general it doesn't work that way. In general, you don't control the thickness; rather, it is what it is, depending on such factors as the thickness of the steel and its silicon content. But you haven't explained the exposure conditions either. What would you consider a "good result" -- no corrosion in 3 years or none in 50 years? Thanks.
Regards,
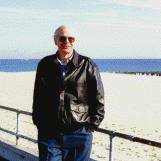
Ted Mooney, P.E.
Striving to live Aloha
finishing.com - Pine Beach, New Jersey
March 8, 2010
March 23, 2010
Sir:
For hot dip galvanizing after fabrication. The products are divided into two categories: 1) Unspecified and 2) Specified. Normally the galvanizer tries to get as thin of zinc coating as possible on unspecified product for economic reasons. Specified product is specified via ASTM or ISO standards and usually a magnetic thickness
(non destructive) gauge is used.
In general there are two types of steel in the market- place:
1)rimmed and 2)reactive silicon semi-killed steels.
Rimmed steels give a bright silver finish in galvanizing and seldom are the coating thicknesses thicker than 4 mils (1 mill = 25.4 microns). With reactive steels the coating thickness increases at a rate of about 1 mil/minute for every minute the steel is in the molten zinc. Thus a piece of reactive steel in the molten zinc for 24 minutes will have about 24 mils of coating (610 microns) on it. Also the reactive steels usually give grey or even blackish coatings. These thick coating may also be subject to chipping off.
Much control of zinc coating thicknesses can be done with proper technology.
Regards,
Galvanizing Consultant - Hot Springs, South Dakota, USA
Q, A, or Comment on THIS thread -or- Start a NEW Thread