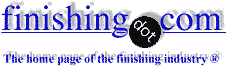
-----
Zinc on steel solution
After researching different ways to treat my steel parts, including building my own hot dip galvanization pot, I tried something different.
A previous zinc on copper plating solution was prepared by mixing copper sulphate
⇦ on
eBay or
Amazon [affil links] root killer with battery acid
⇦ on
eBay
or
Amazon [affil links]
and water. I remembered I had a few gallons kicking around and decided to dump in a bunch of powdered zinc from the vacuum system on our zinc arc spray line. It boiled and fumed and precipitated out the copper. I used a slotted spoon to strain off the copper and other gunk on the top.
Threw in a zinc boat anode, connected it to a nearby battery charger
⇦ on
eBay or
Amazon [affil links]
and dipped in a piece of CRS carbon steel sheet connected to the cathode. It plated a coating of something pretty quickly. It is like gray spray paint. I presume I plated zinc onto the steel.
Right now the part is baking in the oven over a pan of salt water....
To do this right, in a low volume industrial application, will my plating solution do? I realize I need to degrease and pickle. But for plating I know there are brighteners. I am going to try some sugar. But so far, I think I have a cost effective way to apply a anti rust coating on steel.
Advice would be most welcome.
manufacturer - Tooele, Utah
March 7, 2010
You said "to do this right". But your description doesn't really correspond with "doing it right". Mixing old process chemicals with root killers and battery acid ⇦ on eBay or Amazon [affil links] isn't the way to begin.
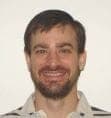
Jon Barrows, MSF, EHSSC
Kansas City
March 9, 2010
We start each process in our company with a "proof of concept" experiment and this was simply our way of demonstrating to ourselves that a zinc coating could be applied with electricity as well as by hot dipping or arc spraying. We are neophytes to this process and are interested in any recommendations of books or consultants, or any advice we can get here about the "right" way to approach this process.
Chuck McCownmanufacturer - Tooele, Utah
March 10, 2010
March 10, 2010
Hi, Chuck. I am linking to a list of recommended plating books that we call our "must have" book list. Also linking to our list of consultants who sponsor the site.
Sorry that I was busy last week and did not respond yet. Yes, you must degrease and pickle. If your parts are hardened steel, you must bake for hydrogen de-embrittlement after plating.
But 99 percent of domestic plating shops buy their zinc plating solutions and zinc plating anodes from industry suppliers rather than trying to formulate their own for a number of reasons including purity, for a deposit that will resist corrosion in salt spray testing reliably; freedom from lead contamination which can jeopardize your wastewater discharge permit and perhaps get you into RoHS trouble; access to proprietary brightening agents and levelers that are consistent and function across the current density range; traceability that will permit ISO and other quality registrations; laboratory analysis by seasoned professionals; and assistance when things aren't going right. Zinc plating must be chromated, and in these days of RoHS, that means trivalent chromate, and I know of no non-proprietary formula for modern trivalent chromating.
It is perhaps not impossible to achieve satisfactory, repeatable, and reliable results with home-brew, but it is difficult enough that the more experience a shop has, the less likely they are to try it. So, while I would try to get some good books and look around for a good consultant, in the meanwhile I would talk to some suppliers of zinc plating processes. Look in our Chemicals Directory, or the yellow pages of a large nearby city. Good luck!
Regards,
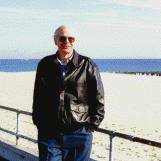
Ted Mooney, P.E.
Striving to live Aloha
finishing.com - Pine Beach, New Jersey
March 11, 2010
Thanks Ted,
EPI / Electrochemical Products Inc. [a finishing.com supporting advertiser] is sending me some chemicals to try.
Do I have to chromate? I was hoping to pull it out of the electroplate tank, rinse off and ship. Cosmetics are not important. Also, yesterday I expanded the experiment. I had a sodium hydroxide saturated solution for degrease, followed by water rinse, followed by hydrochloric acid pickle and then into the plating bath. The part had been through a mechanical deburr tumbler prior to this and appeared to be very clean. But somewhere along the way it picked up what appears to be a black scale in some areas, and would not plate in those areas. The part had been plasma cut from 1/2" plate CRS. Perhaps we didn't get the coating off in the tumbler good enough?
Chuck
(BTW, it has a small tube/pipe of 1.6" dia as part of the assy, will I be able to plate inside)?
Ordering some books now...
- Tooele, Utah, USA
Hi, Chuck. Zinc is a very active metal, quite prone to white rust. I can't say that you "have" to chromate, but in a career of over 40 years spent in plating shops I don't think I saw a single zinc plated part that wasn't chromated (or post-treated in a non-chrome substitute).
As for the problem of black areas, the reason that plating shops follow rigorous written protocols for temperatures, concentrations, immersion time, voltages, etc., is that it's much much easier to produce defective parts than good parts. Not trying to blow you off, Chuck, but when you do "roughly this" and "roughly that", you are not going to produce consistently satisfactory parts. So when you ask what you are doing wrong, the only answer is that you are not plating to specifications. The black could be smut from over pickling; it could be burned on oils that your cleaning protocol doesn't remove; it could be plasma distorted surfaces that weren't fully tumbled off, it could be extreme burning in the plating tank due to too low zinc concentration or insufficient acidity; it could be copper contamination since this used to be a copper plating solution; it could be iron contamination.
Ask EPI for an electrocleaner, a zinc plating solution, and a chromating solution. In addition, send them a few parts and they will plate them and tell you what to do. Good luck!
Regards,
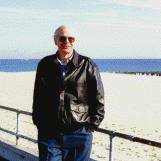
Ted Mooney, P.E.
Striving to live Aloha
finishing.com - Pine Beach, New Jersey
March 11, 2010
Q, A, or Comment on THIS thread -or- Start a NEW Thread