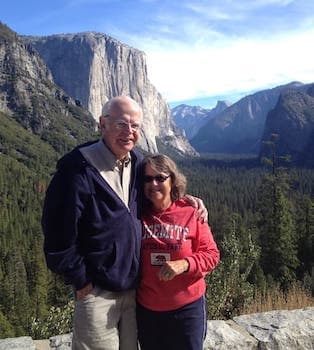
Curated with aloha by
Ted Mooney, P.E. RET
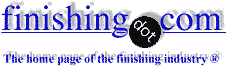
The authoritative public forum
for Metal Finishing 1989-2025
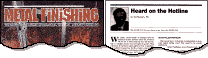
-----
Why does chromic acid anodize have excessive white powder residue after DI sealing
Recently we have had some issues with our Chromic Acid Anodize after sealing in DI water. We have checked our test specimens after anodize prior to sealing and they exhibit no evidence of white powder and rough surface. We have tried sealing for less time and at lower temperatures but still have white powder and surface roughness. When we wipe the powder off the surface is shiny and smooth. Our TDS, temp, conductivity etc are all within limits. Corrosion resistance of panels are excellent but paint adhesion will be an issue without wiping every part we process. Any suggestions?
Lynn O'LaneyEmployee/QCT - Victoria, BC, Canada
March 4, 2010
Alcoa's 1956 Aluminite book reports that over 10 minutes in plain D I water does degrade the coating, that this degradation can be prevented by the addition of a small amount of chromic acid. Email back to me and I will FAX you that part of their book. One of my regular clients has given up trying to seal chromic acid anodizing in plain hot water and is switching to Boeing's idea of 25 gm/100 gal Chromic Acid with 18 gm per 100 gal of Sodium Chromate. There are many commercial specs out there that call for hot water sealing of chromic acid anodizing, but it does not work, especially if you stay in the 15 minutes that the Mil spec calls for. Again Alcoa says limit to 10 minutes to prevent degrading the coating.
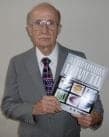
Robert H Probert
Robert H Probert Technical Services

Garner, North Carolina
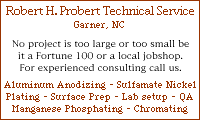
March 8, 2010
Q, A, or Comment on THIS thread -or- Start a NEW Thread