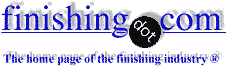
-----
Sanding 439 stainless steel
Our company has recently introduced an appliance part made of 439 stainless. Part of the manufacturing process is sanding to even the edges of the part after forming. The 439 reacts differently than 201 or 304 stainless in that it gums up (or breaks down the abrasive) sanding belts very quickly. We are using a 36 grit ceramic oxide belts. Looking for solutions to a. extend the life of belts, and b. minimize heat generated when sanding.
John HaleEngineering Manager - Athens, Tennessee, USA
March 1, 2010
Well beyond saying that you're sanding stainless and you are having a problem you haven't really told us anything, but for giggles I'll try to guess what you are doing. If you are sanding edges you are probably using some form of upright industrial belt sander like a Baldor 2 x 48 or a knock off in 2 x4 8 or 6 x 48. Soft stainless has always presented problems with belts. The first thing you have to stay away from is heavy cutting as the stainless will gum up the belts regardless what type of belt you use. Some finer grain belts like 120 or 150 will work a bit better but they cut painfully slowly. You should be cleaning the pins out of the belts fairly regularly with a gum bar. Once the belts get some pins in them they tend to gum up even faster. On fine belts I use common chalk as a lubricant and it seams to help clear them a bit but its dusty and a bit of a nuisance. The best thing you can do is slow down the feet per second of your belts. You may be able to do this by changing out your drive wheel or changing the motor to a variable speed model. The best is to go to longer belts and run them slower. This cuts down on heat and at the same time the belts are cheaper per linear foot. I was curious as to why the 2 x 72 inch belts were only a buck or so more than the 2 x 48s which initially did not make much sense to me. The salesman from 3M told me that it's not the belt that you are paying for but the seam that joins the belt together. I don't know if the answer was bullshot or not, but it made enough sense that I stopped asking. Burr King used to make a nice 2 x 72 inch model but overall the Wilton square wheel is probably the Cadillac of belt sanders. With the Wilton you can also add a 2 inch idler wheel to open and close the grain of the belt as it goes over the idler. Clean the belt frequently with a gum bar. Use a chalk or wax lube. Decrease your feet per minute of the belt. Decrease cutting pressure and increase your belt length if you can afford to do it. Last time I checked square wheels were $3000.00 or $4000.00. Burr Kings were about $1600.00 to $2000.00. Mind you even the Baldors are $1000.00 now days. In my exasperated experience aluminum, titanium, copper and stainless are all nuisance materials when it comes to grinding.

Rod Henrickson
gunsmith - Edmonton, Alberta, Canada
March 5, 2010
Q, A, or Comment on THIS thread -or- Start a NEW Thread