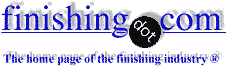
-----
Coating sodium metal with T6 aluminum, beryllium copper, Invar and/or molybdenum.
I am the inventor of sodium electrical wire, described in US patent 7,626,122: www.freepatentsonline.com/7626122.html. It is an electrical wire that safely conducts electricity at 1/3 the electrically equivalent weight of copper.
I am evaluating the most economical means of mass producing this lightweight wire, one of which may be via selective electroplating. However, I know very little about electroplating. Assuming such an approach is feasible, I am interested in purchasing a turn-key continuous reel-to-reel production line that can efficiently turn out kilometers of wire per day around the clock.
I wonder first of all if it is even practical to electrically coat sodium metal with any structural metal. Secondly, I wonder what kind of limits there are as to what alloys the sodium could be coated with. Elemental molybdenum, copper and aluminum could be used, but the wire would function best with strong, electroconductive, lightweight springy alloys such as T6 and beryllium copper. In operation, the sodium core of the wire is designed to repeatedly melt around 97 C, so coating alloys that are corroded by molten sodium are undesirable. I know that beryllium copper is highly resistant to sodium at operational temperatures. I am not so sure about T6, although pure aluminum appears to be adequately resistant, as indicated by the aluminum/sodium binary phase diagram.
Using an electroplating approach, the finished wire would probably not have the same exact forms shown in the patent drawings. The simplest embodiment would be a ~3 mm diameter circular sodium core surrounded by a ~32 micron shell consisting of an ~11 micron beryllium copper layer and an approximately ~21 micron T6 aluminum layer. Going around the circumference of the shell, the order of the layering of the aluminum and copper alloys would switch four times. That is, in the first and third quadrants of the circular circumference, the aluminum alloy would be on the inside, whereas in the second and fourth quadrants the beryllium copper would be on the inside. This screwy alternation of the order of the layers around the circumference is required to take advantage of a bimetallic effect that bends the wire wall when the temperature of the wire increases.
So, to summarize, if possible I would like to continuously and and selectively coat T6 onto sodium, BeCu onto sodium, T6 onto BeCu, and BeCu onto T6.
Inventor, developer - Bronx, New York, USA
February 25, 2010
March 4, 2010
The idea of sodium wire intrigues me. Sodium being so reactive doesn't this represent a significant health risk, particularly if the coating cracks and moisture gets in?
Anyway to answer your questions. T6 is a temper state and to get the material to that temper state it needs to be heated through 2 stages. The first at approx. 500 °C and the second at approx. 190 °C. So that probably rules out using T6 next to something designed to melt at 97 °C.
Electroplating could be even more fun. (And when I say fun I mean fun for those stood 1-2 miles away watching the fireworks). Isn't sodium very reactive with water because most plating happens in aqueous and acidic solutions or have you done something to the sodium to stop it reacting in this way.
Aerospace - South Wales, United Kingdom
March 4, 2010
Sodium metal can indeed be a possible health risk. It explodes on contact with water to produce hot exploding hydrogen gas and caustic sodium hydroxide steam. It can burn in air to produce a caustic cloud that dissolves a person's lungs. I hate when that happens.
My invention gets around these problems by encasing the sodium in a special shell. If the wire is cut, the remaining shell instantly springs out laterally to suck the sodium deep into the wire, away from the break, before the sodium can react with the environment. The sodium is thus kept away from air, water, or whatever else it might otherwise react with. At the same time, the insulation of the wire protracts over the cut to seal the hole. Basically, the wire is a machine that heals itself when cut.
I was hoping for a method to somehow electroplate the various components of T6 (or similar alloy). Then, in a subsequent bending step, cold working the coating to a high temper, making the shell as springy as possible. However, a method that can coat only a single element such as magnesium, aluminum, copper or molybdenum would be very useful.
However, tempering via a heat treatment would seem to be theoretically possible, assuming the sodium can first be coated with a material that can withstand the subsequent temperature of tempering without dissolving in the sodium. A strike of molybdenum, for example.
Such a refractory strike would serve to contain the hot molten sodium while outer layers are tempered. Sodium vaporizes around 883 C, but even a tempering temperature above that would be theoretically possible if only a small segment of the wire is tempered at a time. The sodium vapor would travel from the hot region of the wire to colder regions, relieving the pressure.
I realize electroplating sodium metal with anything "is not done" in the finishing industry. There normally is no need for such an oddball finishing operation. If it can be done at all, it is probably a rather tricky operation. If someone developed such a technique, it would be useful outside of my application. For example, beads of sodium could be encased in such a coating, increasing the safety of industrial sodium during transport, decreasing shipping costs.
You pinpointed out a major challenge to electroplating sodium. As you point out, plating in an aqueous solution, although making a great fireworks display, would not be very effective, because sodium reacts violently with water. Even a trace of water in the coating solution would end up contaminating the sodium with sodium hydroxide, which increases the corrosion rate of the shell. Some sort of a non-aqueous solvent would be needed that is not reactive with sodium (probably polar so as to help carry metallic ions, but halogen-free to prevent spoiling the sodium cathode). There aren't that many such choices of solvent, because sodium is very reactive with almost everything. I know sodium is commonly stored in kerosene and naphtha.
It would seem there is no "recipe" for coating sodium. I think it is an unusual and challenging electroplating problem that brings up a lot of issues.
- Bronx, New York, USA
"It would seem there is no "recipe" for coating sodium. I think it is an unusual and challenging electroplating problem that brings up a lot of issues."
Indeed, that is the crux of your problem. I suspect that you will find no one here or anywhere else who has an answer to your query.
You might as well ask how to transform iron into gold or how to create perpetual motion. If any alchemist DID know the answer, it would not be shared gratis.
Good luck.
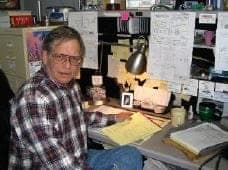
Jeffrey Holmes, CEF
Spartanburg, South Carolina
March 5, 2010
March 9, 2010
The idea of a sodium core was in use in the 1930s (albeit for heat conductivity rather than electrical) for valve stems, notably for the famous Merlin engine in the Spitfire, and is still going strong today.
Old age has made me wary of declaring anything impossible but I would suggest that the probability of an economic process to electroplate onto sodium is asymptotic to zero - if not less.
Not only does sodium react with water but also with organic compounds; much more readily than aluminium for example.
I would suggest that the only likely way forward for a manufacturing process would be co-extrusion. Sodium is easily extruded in wire form. If you visit your local organic chemi lab they will make some while you wait. Extruding the sheath requires more power but is well developed (copper tubing, lead sheathed cable etc are made this way)
So - for development anyway - slide sodium wire into copper tube and run it through sizing rollers, (any manufacturing jeweler will have these)
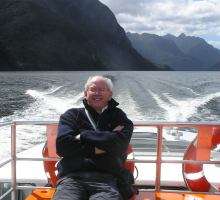
Geoff Smith
Hampshire, England
March 10, 2010
I also don't like to declare anything impossible until proven impossible. That is why I am pursuing multiple methods, keeping an open mind to possible unconventional means of manufacture.
THF (tetrahydrofuran) is a known non-aqueous polar solvent known to be compatible with sodium. Maybe THF could carry metallic cations to a sodium cathode. Are there any chemists out there who can say why it can't?
I agree the preferable method of large-scale manufacture appears to be co-extrusion, specifically the microfluidic continuous casting method disclosed in my patent. But the nanofabrication of the hardware is very expensive. Hence I am looking at other ways.
The big problem with ordinary extrusion of solid metals is that it is hard to get a uniform tube wall less than 0.4 mm. Sure, with enough power you can push anything through a die. But that doesn't mean that it will come out smooth. The walls of my wire have to be an order of magnitude thinner than 0.4 mm. However, by extruding stabilized liquids via the microfluidic continuous casting method, it is possible to extrude extremely thin distortion-free walls. But again, only with expensive micromachined tooling.
Using sizing rollers is a great idea for prototyping, and it might even be a good method for mass production. The nice thing about sodium is it is as soft as butter. As the roller reduces the size of the harder tubing, the sodium just glides out of the way. It would function as a pot metal to prevent kinking and distortion of the tube. Once I have the sodium hermetically protected in a structural metal, conventional electroplating techniques are available to selectively coat the tube.
One potential problem with stretching a tube is that I can't get the walls thin enough. The walls might also stretch in a non-uniform manner. The thickness of the layers in the metal wall must ultimately be carefully calibrated in order for them to properly curve when the wire is heated so as to properly retract sodium away from any break. If a layer is only a few microns too thick or too thin, the wire won't work right. However, there are ways around the problem of distortion caused by rolling. Hmmmm.
You've given me some nice ideas that could quite possibly save me a lot of development time. Thanks, Geoff.
- Bronx, New York, USA
March 19, 2010
David
If you are still pursuing the organic plating route you may want to take a look at the Transactions of the Institute of Metal Finishing. There is a link on this site or http://www.uk-finishing.org.uk/index.htm
There have been a number of papers on related topics but only on Aluminium as I recall since there is no pressing demand to plate other metals by this route. All are directed at pure Al which will not give you the T5 condition.
Plating alloys is possible but I know of no work in this field from organic solvents.
Some commercial Al plating has been attempted but the process is reported as anything from difficult to '#%%5! dangerous.
Plating onto Na wire could actually simplify this as you could possibly extrude the Na directly into the plating cell and work with a closed system and also have a nice clean surface to plate onto.
The field appears to be entirely yours. Please let us know how you get on. Good luck.
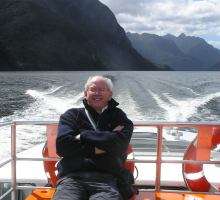
Geoff Smith
Hampshire, England
Hypodermic needle manufacturers may have a clue about how to control thin walled tubes. It could be worth talking to some of them. Good luck,
Guillermo MarrufoMonterrey, NL, Mexico
March 19, 2010
March 26, 2010
Actually, I have looked at the websites of needle tube manufacturers. The problem with off-the-shelf needle tubing is that the walls are way too thick. I need walls on the order of 32 microns thick (about 1 mil), but needle tubing walls are usually at least ten times thicker than that. Furthermore, I would optimally have very precise thickness dimensions (± 1 micron).
I suppose I could start with some needle tubing and carefully grind down the wall thickness, but that would be a rather laborious process and I am not sure I could achieve the kind of uniformity of wall thickness that I would like.
It seems to me that, at least theoretically, electroplating is potentially the best way to achieve extremely precise layered thicknesses.
If there were a process to apply a strike layer of almost any common metal onto sodium, then I could apply additional layers on the strike by conventional known means of selective electroplating.
- Bronx, New York, USA
Geoff, that is a nice lead. I'll look into research regarding plating onto aluminum with organic solvents. Maybe those techniques could be adapted. At least there might be a discussion of the theory of what works and why, as well as what can't work and why.
It would appear, as you say, that there is no recipe out there for electroplating sodium. That doesn't necessarily mean that it is especially difficult or impossible to do. Most likely, no one has had any need to bother figuring out how best to do it.
I'll probably eventually end up running a few experiments guided by the theory of plating aluminum in organic solvents.
It was my intent, as you suggest, to directly extrude a sodium wire into an electroplating solution under an inert environment. The surface of the sodium would indeed be very pure straight out of the extruder, without any need of further cleaning.
I don't need to directly plate any particular alloy onto sodium. A strike plating of almost any common metal onto sodium would suffice. Once I do that, it should be cookbook electrochemistry to selectively plate additional layers.
- Bronx, New York, USA
March 26, 2010
David, in case you haven't already found them, there's an outfit in Minneapolis that commercially electroplates aluminum using an organic solvent. AlumiPlate is their name, and they have the obvious website.
Good luck!

Lee Gearhart
metallurgist - E. Aurora, New York
March 31, 2010
David
You may like to consider a seminar next month which reports an EU funded project on plating from ionic liquids.
www.uk-finishing.org.uk/seminars.htm
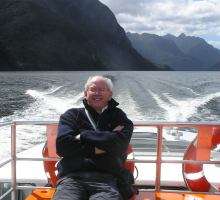
Geoff Smith
Hampshire, England
April 3, 2010
Lee, that is a good lead. I shot them an email. Maybe they already have a process that would work, or can explain why it doesn't work. Once I have a strike layer of aluminum, then more conventional techniques can do the rest.
Geoff, I'll check out that seminar. Maybe there will be something useful there. Thanks.
- Bronx, New York, USA
April 9, 2010
David,
Read your conversation with interest AND thought maybe you could consider a refined powder coating technology applications for your reel to reel coating concept.
Am not involved in production sciences but the temperatures may be compatible and even the flexibility/ safety requirements might be met if additional layers of flex-sealing materials meeting your advanced needs were applied in a secondary process.
It would be interesting to hear more, especially about your targeted application for this material wire.
Jim
student - LOS ALAMITOS, California, USA
January 27, 2011
October 21, 2016
This is a really old thread, but it might work using ionic liquid methods. See Bakkar (2015) "A new method for practical electrodeposition of aluminum from ionic liquids".
I've fooled with this method and it works okay (I did it quick and sloppy though). A beauty of this method is you can prepare your electrolyte in a controlled atmosphere, put a layer of decane over it, and then perform electrodeposition in ambient atmosphere. Also the chemicals involved aren't nearly as dangerous as those involved with other Al-plating methods.
If you're still involved with your LLC and this passion please reply.
The Ohio State University - Columbus, Ohio USA
Q, A, or Comment on THIS thread -or- Start a NEW Thread