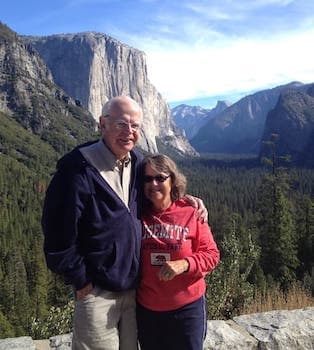
Curated with aloha by
Ted Mooney, P.E. RET
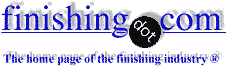
The authoritative public forum
for Metal Finishing 1989-2025
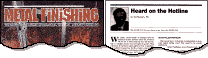
-----
Copper Plating Teflon or Similar Plastics to Allow Soldering of Wires to it
February 19, 2010
I currently am working on an electrical antenna project where I need to plate/coat a Teflon conic profile. Here is a picture of the profile that needs to be masked and plated:
I need to solder wires at the base of the conic cones (there is a cone at each end so the part is symmetric in profile).
So I have a few questions:
I've investigated electroplating plastics and have been running into problems due to non-conductive surfaces and possible contracting and expanding of plastics which causes the copper plating to flake off. First off, I haven't found anyone that seems to have a solid solution to plating copper on plastics or even Teflon for that matter.
From what I've gathered and been told, it sounds like if an electrically conductive paint is first applied, then using the conductive surface to attach the anode to, the standard electroplating process to copper plate the parts should work. Another problem, one local plating company said is they sprayed the ABS plastic part with copper paint, tried their standard copper plating process and the heat caused expanding and contracting of the plastic to the point that the copper plating bubbled and started to flake off.
However, ABS plastic has a much lower melting point than Teflon(Teflon has a melting point of 680 degrees F) so I don't think the expanding/contracting will be an issue with Teflon.
So does anyone know if I can plate Teflon?
Furthermore, I'm also wondering if the copper paint that you can buy in spray cans or brush on would be applicable and could withstand the temps from a soldering gun which is around 450 degrees F. Anyone have any recommendations for paints that might work? I've found a silver and nickel paint from a company called Action-Electronics, here is the link to the silver/nickel paint product: action-electronics.com/conductivepaint.htm
If someone could please help I've got to get this project done for a customer (a very large camera company) and need some guidance ASAP.
Thanks
Josh HilgartProduct Development Engineer - Cardiff, California, USA
February 28, 2010
Teflon/metal composite tape is sold on the market. I have seen both aluminum/Teflon and copper/Teflon. Teflon/metal tape comes with and without adhesive.
Maybe you could start with the composite tape, deforming it into a cone by pressing it. The thinnest Teflon/metal tape you can find would be more likely to stretch into a cone with the least distortion. The metal layer might become uneven in thickness, but it might serve as an adequate layer for subsequent electroplating. Aluminum/Teflon probably stretches more than copper/Teflon. There is a greater variety of sizes and formulations in the aluminum/Teflon than copper/Teflon.
Contrary to popular belief, there are ways to glue Teflon to metal. There are adhesives and kits on the market to do this. You might look at gluing a copper foil cone to Teflon rather than attempting to directly electroplate Teflon.
- Bronx, New York, USA
First of two simultaneous responses --
Many years ago they used metallic sodium to etch the teflon so that it would take a special glue.
A lot will depend on whose proprietary process you use, how good you are at it and how much abuse will the part take.
- Navarre, Florida
March 1, 2010
Second of two simultaneous responses --
As you may already know, the key to successful, well adhered plating on plastics is a mechanical grip that is most often provided by means of an acid etch to specifically formulated resin blends that have globules of an acid sensitive compound that dissolve preferentially, leaving minute anchoring pits after the etch. Teflon is a homogenous resin and extremely resistant to most chemicals, so, a preferential chemical attack is close to impossible. Perhaps you need to investigate laser etching or micro machining to provide an acceptable surface. The roughness has to be of the locking type (similar to fish hooks or dovetails).
Guillermo MarrufoMonterrey, NL, Mexico
March 1, 2010
Mylar and other polymer films are metallised by vacuum evaporation. These are used in package industry as well as in making capacitors. There are two differences. First, you need copper while generally aluminum is used for metallisation. But this is not a problem except that you need higher temperature for evaporation. Second is the substrate. Teflon is more hydrophobic than mylar etc. Perhaps it needs more intense plasma treatment before coating. I suppose it is worth trying if you have not already found a solution. Simple vacuum evaporation can be replaced by magnetron sputtering. In either case one should ensure the substrate is not heated too much.
H.R. Prabhakara - ConsultantBangalore Plasmatek - Bangalore Karnataka India
March 5, 2010
April 12, 2010
J. Hilgart,
Have found surface preparation for plating plastics to be either proprietary or patented processes. Teflon is an extremely difficult material to plate. I am currently searching for a plating company to plate copper onto the interior and exterior surfaces of a PVC pipe substrate. The basic process for my requirement is as follows:
A mask is applied to the device/component and the component is flashed with let's say copper in an electroless plating process. The mask is removed and the copper deposition is continued to the required surface thickness in an electroplating process. However, surface chemical preparation is critical to adhesion of electroless plating to the surface of the component. I too need to attach through a soldering process, copper strips, not wires, but our applications are very similar. Mine even more so, in that soldering melt temperatures will deform the PVC under the solder joint. That's all I can contribute.
Best regards
Tampa, Florida, USA
Q, A, or Comment on THIS thread -or- Start a NEW Thread