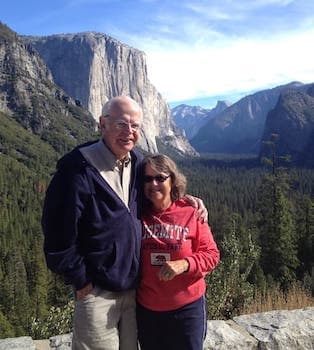
Curated with aloha by
Ted Mooney, P.E. RET
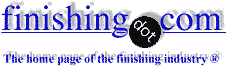
The authoritative public forum
for Metal Finishing 1989-2025
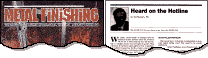
-----
Thin film, dry type, corrosion resistant treatment after nitriding
We look for a treatment which can withstand corrosion protection of 72-96 hours after nitriding. The treatment shall be of dip type with thin (< 10 microns) and dry type coating. The parts are made from spring steel with hardened and tempered.
Narasimhun Parthasarathyprocess designer - Chennai, Tamilnadu, India
February 18, 2010
February 22, 2010
Dear Narasimhun Parthasarathy,
Your question is not clear?
which type of nitriding you are doing for your parts?
If you are doing Carbonitriding with more than 0.25 mm
depth, do any Mos2 based or PTFE coating with alumina blasting with low pressure (please be assured your case depth and hardness are with in the spec after coating) for your parts.
If you are doing Gas or Salt bath nitriding, add the Oxidation process after nitriding for your requirements.
Or dip it in resin sealant for better corrosion.
In my opinion, for the Heat treated spring steels, zinc plating in Electrical method is not advisable for hydrogen embrittlement.
- Salem, Tamil Nadu
February 24, 2010
Presently we do dip spin process using zinc aluminium coating process for springs. During this process, we face issues with solid particles bridging the helical springs and resulting in product output variation.
Hence, we are exploring possibility to carryout nitrocarburising in gaseous atmosphere. In order to achieve NSS requirement of 72-96 hours, we need a thin film, dry type wax coating which should not impact on the performance. We cannot carryout PTFE, Xylan, liquid painting etc., and the choice of plating is eliminated due to hydrogen embrittlement issue.
Appreciate your valuable input in this regard.
- CHENNAI, TAMILNADU, INDIA
February 25, 2010
Dear Narasimhun Parthasarathy,
I don't think Nitrocarburising will help for the springs,
Maybe better you continue the Same dip and spin method, with continuous filtering the Bath and keep a small Magnet Plate on bottom of the solution bath, or if the base preparation is Blasting, do the solvent degreasing after the Blasting, if the base preparation is phosphating, do the phosphating with Smaller particle size.
- Salem, Tamil Nadu, India
Q, A, or Comment on THIS thread -or- Start a NEW Thread