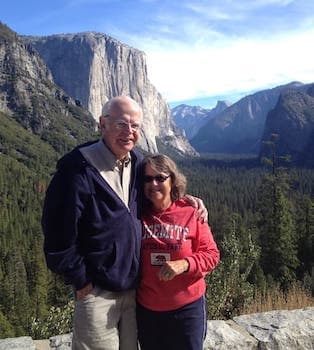
Curated with aloha by
Ted Mooney, P.E. RET
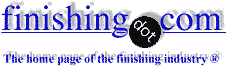
The authoritative public forum
for Metal Finishing 1989-2025
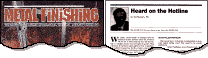
-----
Real-time thickness data collection on pipe galvanizing line
We operate an automatic galv plant for steel tube and pipe in a size range from 1/2" to 4". I am looking at measuring and improving the process capability to get a more even coating. Ideally I would like to get at least one data point for each tube as it comes out of the bath. Possibly something like a pneumatically operated ultrasonic probe on the steam blow-out, interfaced via RS232 to a PC ... has anyone ever done this? If so, what were the snags and successes? Is it robust enough? What did you learn in the process?
Thanks!
production engineer - Johannesburg, South Africa
February 4, 2010
Sir:
During the 1980's I consulted for the largest galvanizer in Johannesburg and for their three pipes galvanizing plants. The most interesting part of pipes galvanizing is the zinc thicknesses on the INSIDE of the pipes. I recommend that you do i.d. profiles. The thickest zinc coating is usually about one-third from the top
(blowing end). Initially these coating thicknesses were around 200 to
300 microns. By switching flux formulation this i.d. zinc thickness was reduced to 20 to 40 microns. Thus your focus on the o.d. coatings seems to be in the wrong place. I have technology to give very thin zinc i.d. and o.d.(too thin for most water pipes). I also have technology to give even and smooth, uniform i.d. zinc thickness for large bore pipes with about 10% the steam blow power.
Regards,
Galvanizing Consultant - Hot Springs, South Dakota, USA
February 5, 2010
September 14, 2011
Through proper control of flux: pH around 4, baumé scale around 20-25 + some good wetting agent then dipping for enough time and drying.
Through proper control of galvanizing bath alloy: 400-600 ppm Ni, 20-40 ppm Al. No need for lead, Bismuth, Tin. Temp:450-460 degrees C.
Through standard blowing pressure and temp. it is possible to get coating thicknesses around 20-40 microns.
HOT DIP Galv. - Istanbul, Turkey

Q, A, or Comment on THIS thread -or- Start a NEW Thread