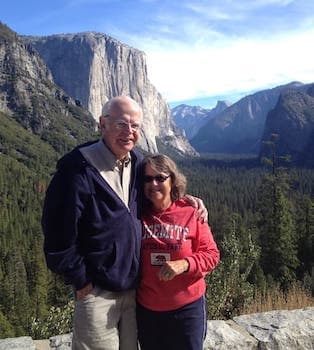
Curated with aloha by
Ted Mooney, P.E. RET
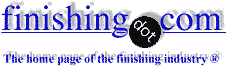
The authoritative public forum
for Metal Finishing 1989-2025
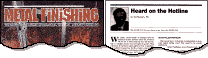
-----
Zinc vs. Nickel Plating, and Rack vs. Barrel
Dear All, I am a little confused about some of the answers on this site about nickel vs. zinc plating. Can you please help to clarify the corrosion resistance of nickel plating versus zinc plating? While visiting some plating facilities, I have seen barrel plating and "hanging" plating (if you know what I mean, sorry for the lack of a better term: when you suspend all items to be plated on a hanger, and dip them in the plating tank), for both zinc and nickel. It seems to me zinc plating, with barrel plating, is as good as nickel hanging plating, in terms of corrosion resistance; this is our result. We notice the surface finish of nickel plated parts being of a superior quality (mirror-like) than zinc plated. Because the parts we are plating have to have both cosmetic appeal and corrosion resistance, I am curious to know what is your experience in this respect. Thanks in advance.
Luca Gandolfosporting goods - Portland, Oregon
February 3, 2010
February , 2010
Hi, Luca. The "other" way of plating that you observed is called "rack plating".
The usual reason for barrel plating instead of rack plating is labor savings because thousands of pieces can be put in a barrel without laborious individual racking. But barrel plating can offer some additional advantages like more consistent plating thickness and freedom from rack marks (small spots where there is no plating because the electrical connection was made there). Some items are too big or too fragile to bang around in a rotating barrel though.
Yes, nickel plating is considered by most people to be more attractive than zinc plating, but it is usually substantially more expensive.
The big advantage of zinc plating from a corrosion resistance standpoint is that it is anodic to steel (it offers cathodic protection), whereas nickel is cathodic to steel and accelerates the corrosion of steel via galvanic action if any steel is exposed. Consequently, nickel plating is sometimes said to be a "barrier layer" plating. If you could afford to put exceptionally thick nickel plating on the parts, it would be reasonably corrosion resistant, but you usually can't. Often the plating will have or will get tiny pores which expose the steel to this galvanic action. Good luck.
Regards,
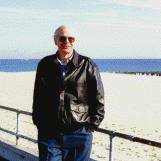
Ted Mooney, P.E.
Striving to live Aloha
finishing.com - Pine Beach, New Jersey
February 14, 2010
.....nickel metal is about 3-5 times more expensive than zinc.
Today's zinc processes are widely used in areas where it is not only wished with it's excellent protection nor as well as for it's decorative possibilities and anti-allergic properties.
Best regards,
Dominik
- Syndey, Australia
You can try salt spray test as this is the standardized test method to check corrosion resistance of coated samples. Nickel plating and zinc plating can provide corrosion resistance but consistency of plating thickness on all parts plays a very important role. Generally, tiny pores can be observed on areas with low current density and often on recessed areas. Thru salt-spray test oxides is evaluated after a period of time. The more corrosion resistant the coating is, the longer the period in testing without showing signs of corrosion.
Zenaida R. Adorablemetal finishing service - Chemist - Manila, Philippines
February 27, 2010
March 1, 2010
The first question that I would ask is-what is the environment that it will be used in?
The second is- How long do you need it to last before it is junked?
Case ind point, A few years ago is saw a bright zinc plated dog leash chain that had a bright blue-clear chromate applied. These leashes rivaled most chrome plating for surface and luster.
Zinc can work in many cases if you find the right plater. A slop shop will give you sloppy work regardless of the metal applied.
- Navarre, Florida
Q, A, or Comment on THIS thread -or- Start a NEW Thread