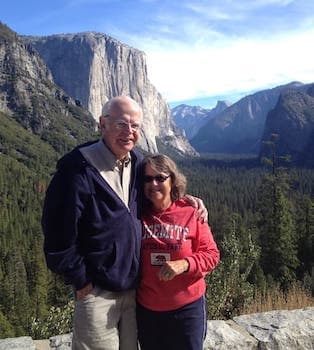
Curated with aloha by
Ted Mooney, P.E. RET
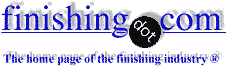
The authoritative public forum
for Metal Finishing 1989-2025
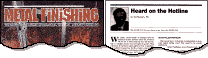
-----
Which stainless steel grade suitable for Bus Shelter ... 304 or 316 ?
We are planning to make 400 Bus Shelters in my City. Some suppliers offer 304 grade of stainless less were the other offer 316 grade of stainless steel ? we are very concerned about the corrosion resistance . which one of them is the most suitable for the Bus Shelters in very high hot and very high Humidity ?
Abdallah AlzariTravel - Sharjah, U.A.E.
January 29, 2010
Hi, Abdallah. 316 is more corrosion resistant but more expensive. Don't forget to have it passivated so it doesn't rust.
Regards,
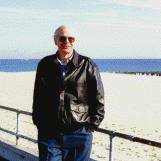
Ted Mooney, P.E.
Striving to live Aloha
finishing.com - Pine Beach, New Jersey
Febuary , 2010
Salem aleikum Abdallah,
over the last years we did several tests with stainless steel and many various surface treatments in the region. In your case 316 electropolished, or even 304 electropolished will last. Electropolish stainless steel has higher corrosion resistance, easier cleanability and a attractive appearance.
- Holland
February 2, 2010
Maybe Edmonton transit is just cheap, but our bus shelters are all made of fiberglass, Plexiglas, aluminum framework and pop rivets. I have never seen one corrode or rust but they sure explode when a car crashes into them when it's -35 Fahrenheit! Mind you I don't suppose a stainless steel one would fare much better.

Rod Henrickson
gunsmith - Edmonton, Alberta, Canada
February 2, 2010
February 4, 2010
Dear Abdallah,
Most important is that you electropolish your stainless steel for outdoor applications.
It is correct that 316 has a better corrosion resistance than 304, but if you do not electropolish it, it will also rust in your application. 304 and 316 in combination with electropolishing give an excellent corrosion resistance.
Kind regards,
- Diksmuide, Belgium, Europe
Dear Abdullah
I concur with the other respondents. Electropolished 304 or preferably 316 is what you should be using. Which ever you choose and what mode of passivation you use the key is maintenance. The surface can be very easily contaminated from atmospheric particulates which induces galvanic corrosion and therefore regular washdowns are essential.
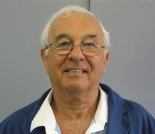
Joel Levinsohn
- Sydney, Australia
February 6, 2010
Electropolishing is good advice. 316 generally fares better than 304 in high-chloride environments, i.e. near a coastline. Regular washdowns with fresh water as Joel mentioned is a good way to delay chloride damage. Keep an eye on it in any event, if corrosion does start, have it cleaned up and repassivated right away.
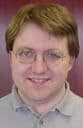
Ray Kremer
Stellar Solutions, Inc.

McHenry, Illinois
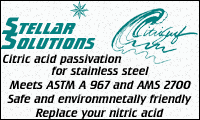
February 9, 2010
Dear Abdallah:
Stainless Steel 304 or much better 316L Electropolished is your best alternative for your job. I completely agree with everyone here. I have something else to share with everyone. We have been in the Passivation Industry for 15 years now and we do apply a passivation process to large exposed surfaces, even after being in use already installed in Position. It's called Swap Passivation, and it's done with a acidic gel that you can apply with a paint brush or similar, it's very easy and environmental friendly (it's made of biodegradable chemicals, and in this way you can re-passivate that surfaces during its service life, lasting for more years without getting corroded or rusted. Good Luck
- San German, Puerto Rico
February 17, 2010

this text gets replaced with bannerText
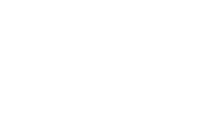
Q, A, or Comment on THIS thread -or- Start a NEW Thread