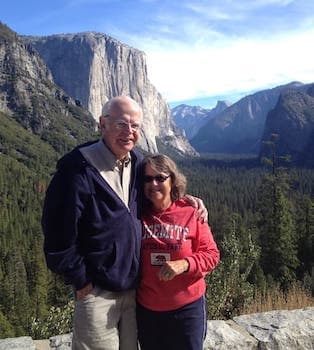
Curated with aloha by
Ted Mooney, P.E. RET
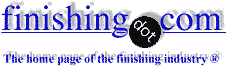
The authoritative public forum
for Metal Finishing 1989-2025
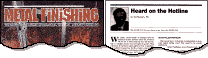
-----
Hard chrome plating parameters

Q. Good evening,
I am currently an Industrial Engineering student in one of the companies that produce water pumps in South Africa. The engineering manager gave me a project to determine the suitable temperatures, the solution strength, the current, the voltage in each chrome tank. The rotors must be chrome plated and then they are assembled in the stators of the pumps. The engineering manager basically needs me to come with a solution regarding a standard time that each specific model of a rotor should be in the chrome tank for. I hope that I make sense.
Please assist.
- South Africa
December 8, 2021
by Robert K. Guffie
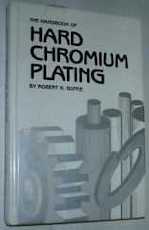
on AbeBooks
(rarely)
or eBay
(rarely)
or Amazon
(affil links)
A. Hi Matsobane. Yes, it makes perfect sense, although I'm not totally sure whether s/he wants you to document the present operational parameters, narrow down on the variations, or design new parameters. The first would be an excellent learning experience, the second would be a great but difficult student project. Obviously, the third, designing new operational parameters, would be a very big job.
Regarding plating time: in general, at a given current (Amperage) per unit of area, the plating thickness will be proportional to the plating time according to Faraday's Law. So please start by telling us how thick the plating is supposed to be. Thanks.
Luck & Regards,
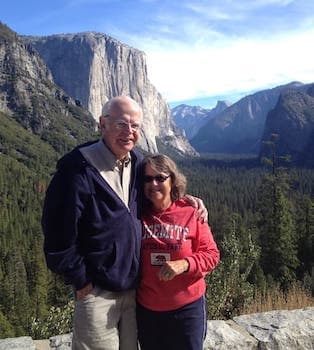
Ted Mooney, P.E. RET
Striving to live Aloha
finishing.com - Pine Beach, New Jersey
December 2021
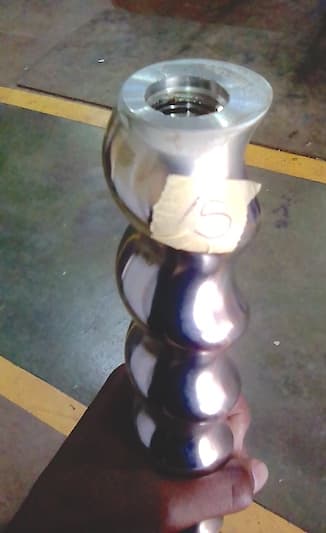
Q. Thank you Mr. Mooney for assisting.
This one rotor that I observed the outside diameter was 52,88 (actual size) after machining. Maximum acceptable final chrome size must be 53,20 (Outside Diameter). 53,15 is the Standard plating size, it was in the chrome tank for 9 Hrs and 15 Mins, temperature 58 °C, 6 V, 2500 Amps. But it was still undersize, meaning that it cannot be allowed to be sent to the assembly section.
Then one rotor, same model that met specification details are as follows: 52,84 outside diameter after machining, max final chrome size must be 53,20, actual size was 53,13, standard plating size is 53,15, same temperature, voltage, amperage. Hopefully I have gave you the full information to assist. I took long to answer because I had to assist in another department Mr. Mooney. Apologies for the delayed response.
- South Africa
December 14, 2021
⇩ Related postings, oldest first ⇩
Q. I am handling a hard chrome plant, and there we do chrome plating on cylinders, rollers etc up to a length of 3.10 metre and diameter 28 inches.
So to save on things, what should be the ideal temperature at which the process should go on and what can be the other methods that we can put in to have better efficiency without compromising of quality.
And is there any way to save on those big electricity bills?
- NCR, India
January 27, 2010
by Clarence H. Peger
(You're unlikely to find this for sale ... but copies are in select libraries)
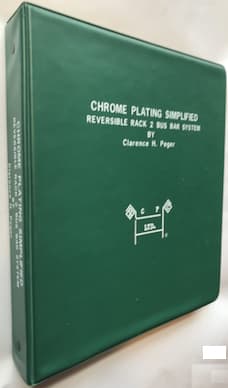
from AbeBooks
* rarely available *
or eBay
* rarely available *
or
Amazon
* rarely available *
(affil links)
A. Hi, Rishi. As you may know, there are several books written just on hard chrome plating. Guffie's "Hard Chrome Plating" is one, Clarence Peger's "Chrome Plating Simplified" is another. When you ask the ideal temperature, the answer for the more conventional approach discussed in Guffie would be about 140 °F, but for the reversible-rack system advocated by Peger as much as 160 °F.
Conventional chrome plating is only about 12 percent efficient, so one way to save electricity might be to try HEEF-25 (a proprietary available from Atotech), which is claimed to be 25 percent efficient (other suppliers also offer this proprietary approach), or to try Peger's idea of higher temperature, closer anode to cathode spacing, and higher current density for greater efficiency. Good luck.
Regards,
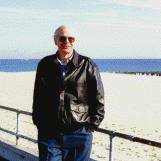
Ted Mooney, P.E.
Striving to live Aloha
finishing.com - Pine Beach, New Jersey
January 28, 2010
Q, A, or Comment on THIS thread -or- Start a NEW Thread