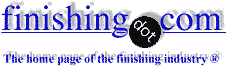
-----
Gold plating on thin Molybdenum wires
We have an inquiry for nickel strike plus flash gold plating on 30 micron diameter molybdenum wires. Most references recommend chromium plating as an undercoat. What role does chromium play here and is it an absolutely necessary step? Also, how does one pass the required current during pretreatments and plating without overheating wires of such thin cross sections?
As the wires are mounted on reels in lengths of around 800 to 1000 meters,a system of continuous plating will have to be designed,keeping in mind all the problems associated with the pretreatment and plating of a difficult material of very thin diameter.We would like to know if any information in this regard can be obtained from references/publications.
product designer - Thane, Maharashtra, India
January 14, 2010
January 20, 2010
Prashant,
Where are all the wire platers out there? Well, I'll give this one a shot. Working with wire platers in the past, the common method was gold over nickel. I haven't experienced wire platers using chrome as an undercoat. There are many factors that determine the line speed. I have seen 1200 ft per minute and gold at a thickness of 30 microinches accomplished with no problem. Today's machine designs can even go faster. Some predetermined factors would be:
1) Diameter of the wire
2) Thickness desired
3) Plating cell size and design.
4) Current density applied
5) Agitation
6) Gold concentration
7) Bath temperature
If you don't currently do wire plating you may want to seek out a supplier that can supply the machine and the entire chemistries involved. This way there is no finger pointing. You can seek out a supplier that has a customer who has similar requirements as yourself. Initially, there is a lot of trial and error in wire plating because there are cleaning, activation, strike, and plating cells that are used. Every process has to work perfectly using the same line speed. All the chemistry has to be formulated for your requirements. Good luck to you.
Fellow Plater - Syracuse, NY USA
Q, A, or Comment on THIS thread -or- Start a NEW Thread