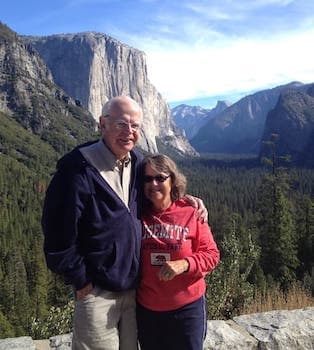
Curated with aloha by
Ted Mooney, P.E. RET
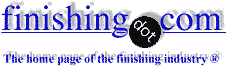
The authoritative public forum
for Metal Finishing 1989-2025
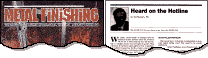
-----
Aluminium addition to Galvanising Kettle

Q. Hello. I have a question about adding aluminum to hot dip galvanizing. According to the data of the American Zinc Plating Association, when aluminum is added more than 0.007%, it is advised not to exceed 0.007% because non-plating occurs due to reaction with flux. If it exceeds 0.007, may I know the reason why non-plating occurs?
LEE KYUNG KEN- Gunsan, Jeollabuk-do, Republic of Korea
October 1, 2021
A. When the workpiece is immersed in the galvanizing bath, the greater the tension on the surface of the galvanizing bath, the less likely the galvanizing bath is to adhere to the surface of the workpiece, and the more likely it is to cause defects such as missing plating. More Al will cause more galvanizing bath tension to prevent plating occurs. For your reference.
Mike WangIntegrated supplier of Galvanizing - Shanghai, China
February 12, 2022
⇩ Related postings, oldest first ⇩
Q1. As one of the most modern fabrication plant here in the Philippines, we also have the largest galvanizing shop. The most common problem that we encounter is on the surface finish of the galvanized item. We traced this to the aluminum content. Please advise us what the exact amount/percentage of aluminum to be used in order for us to have a near perfect finish for all the galvanized products.
Q2. Also, I would like to inquire as to what equipment will be used in order to galvanize bolts and nuts without having it rethreaded after galvanizing. Please advise where we can find said equipment.
Thanks a lot and more power to your webpage.
Best Regards,
Jun C. Capa Production Manager BF Metal Corporation
BF Metal Corporation Manila, Philippines
1999
A2. To galvanize bolts and nuts, without having to 'brush' the threads, you need a centrifuge or 'spinner' This industrial centrifuge spins the bolts inside a basket, at high rpms to remove zinc from threading. In addition, if the bolts are too long to fit into the centrifuge you can do what is called 'rolling'. This is done by rolling bolts (hot out of the kettle) along a 45 degree decline, essentially 'spinning' the excess zinc off as it completes its roll to the ground.
Calvin TowerARS supervisor, finish lead, among other things - Seattle, Washington
May 27, 2022
A Guide to process Selection & Galvanizing Practice"
by M. J. Hornsby
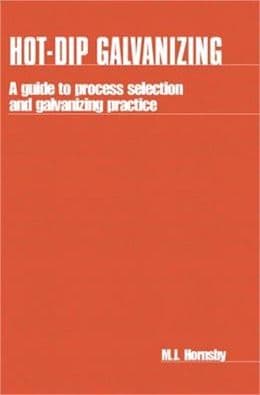
on AbeBooks
or eBay or
Amazon
(affil links)
Q. We are currently adding Al and Ni to out Galvanising kettle using the traditional method.
We have learnt that you have a possible technique that could save us thousands of $ per annum. We are eager to learn more about this.
Galv Service Provider - Adelaide, SA, Australia
January 13, 2010
![]() |
January 15, 2010 A. Steven, Galvanizing Consultant - Hot Springs, South Dakota, USA January 18, 2010 A. Who are you asking your question of, Steven? ![]() Geoff Crowley Crithwood Ltd. Westfield, Scotland, UK ![]() ---- |
by NACE
[only rarely available]
on AbeBooks
or eBay or
Amazon
(affil links)
Q. Thanks for the responses.
1) We are Galvanisers of general products.
2) We use the "traditional" Zn + Al alloy bricks to add Al to our kettle.
3) We were told Dr Cook has technology available to save on Al Addition costs
We have a break from heat waves and thankfully no fires at the moment. Thanks for the concern.
Steven Evans [returning]Galvaniser - Australia
January 18, 2010
Q. I worked in the steel industry for many years. We used Al wire feed into the molten steel as a means to kill the steel. Al has higher affinity for oxygen and reacts with it removing O from steel.
I have no data on costs of capital and or consumables, but this concept should work well in the galvanising industry for adding Al to Zn kettle. We could experiment and develop a similar technique. Being impatient, I would prefer to use proven existing technology.
Is this technology commercially available for galvanisers?
galvaniser - Adelaide, Australia
January 19, 2010
A. Problem is that adding Al to steel is easy (MP steel about 1490 °C, and casting temp typically 1630 °C or so).
But galvanizing temperature is about 450 °C, below melting point of Al.
It will dissolve, but slowly.
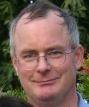
Geoff Crowley
Crithwood Ltd.
Westfield, Scotland, UK
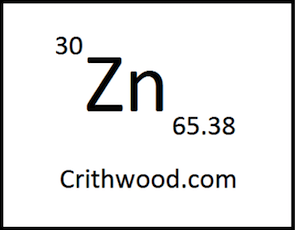
January 23, 2010
January 26, 2010
A. Steven:
From our e-mails and phone conversations you know that I have advanced technologies, a small part of which allows you to never purchase Al/Zn brightener. With the main features of this advanced technology and with proper formulation, control, and use of quadraflux, I expect to eliminate your use of nickel (which according to the CDC causes lung and nasal cancer). In addition, if you follow historic results, the ash reduction and thinner zinc on the product could be substantial additional savings. (World-wide about 150 galvanizers use this advanced technology to advantage beginning in 1992.
[Ed. note: Dr. Cook quantified these potential savings but we have deleted the numbers from the above discussion because Steven may not wish his sizes and production figures which were discussed in private conversation to be publicly posted.]
I have already recommended that at your next kettle change to increase your kettle furnace to 100% firing (10,000 Btu/sq.ft./hour through the side wall heating zone; with proper air/zinc protective insulation to prevent wash-line erosion, and zinc/dross protective insulation to prevent deep kettle burn-through) so as to provide production of about 20 MT/hour. An end-fired kettle gives more production and uses 25% less natural gas. Kettle lifetimes are expected to be 10+ years. By doing this you can galvanize at a reduced temperature and reduce the reaction of the reactive steels.
Also as you know I recommended the acid rinse water treatment system (uses no chemicals; but requires 3KW of electricity to operate) to keep the non-volatile iron (+2) chloride low in your flux to allow short kettle cook-out times. For reactive steels each minute in the zinc gives 25 additional microns of zinc thickness.
The spec. for Al/Zn brightener bar is ASTM 860. Brightener bars can contain ANYTHING, including iron, copper, tin, cadmium, lead, silicon, magnesium, etc. Thus these brightener bars (from unreliable sources) could burn out a kettle, cause thicker zinc on the product, cause more dross, more ash, be toxic, cause white rust, etc.
Ash and dross can contain nickel.
Regards,
Galvanizing Consultant - Hot Springs, South Dakota, USA
Q. I work in a galvanizing wire factory. We galvanize wire of diameter 50 mm to .5 mm. We are using aluminium alloy (ZAMAC 3 containing 3-4.5% Al) to add brightness to the wire.
I wold like to know the % of aluminium that must be maintained in zinc bath. At present the aluminum % is 0.01%.
galvanizing company - Chennai, tamilnadu, India
January 15, 2017
A. If you are not facing any problem in process of Galvanizing, then let it be at 0.01%. As such, apart from specifications, Galvanizers are using up to 55% Al in Zinc Kettle (Galvalume).
Umesh DalelaGalvanizers & Consultants - Delhi, India
January 18, 2017
Why can't we add pure aluminum to galvanizing kettle?
Q. I have one question please,
Why should we using alu/zinc alloy?m i mean what is the problem of adding pure aluminum directly to the kettle?
- Jeddah, Saudi Arabia
November 22, 2020
I once knew of a plant that added pure aluminium in error. Ended up with excess %Al (about 3% if I remember), and the whole kettle contents was unusable and had to be pumped out.
In theory there's nothing to stop adding pure Al, but the solubility is lower than in the 5%Al 95%Zn alloy. It won't melt (Al MP = 660 °C, versus Zn 419 °C, and kettle temp probably 450C), but will slowly dissolve. So this is more like adding rock salt to hot water - doesn't melt, but slowly dissolves.
It's less controllable in end result, and slower, so why choose the hard route that gives unpredictable results?
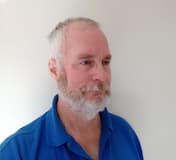
Geoff Crowley, galvanizing consultant
Crithwood Ltd.

Bathgate, Scotland, UK
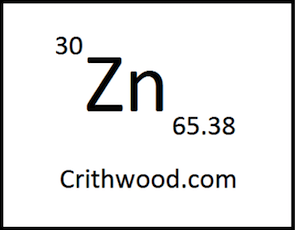
November 26, 2020
Q, A, or Comment on THIS thread -or- Start a NEW Thread