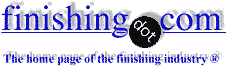
-----
Salt spray test on assembly - galvanic corrosion problem
I'm providing a zinc+clear chromate plated fastener for an electronics application per my customer spec, but it fails miserably during a 96 hr salt spray when it is on the assembly. It passes the test fine on its own. The male stud is unplated bronze and the electric terminal being clamped is phosphor-bronze with tin coating. The nut is very small (M2 X 0.4) so I am concerned if either tin or nickel are going to be too thick to apply to the nut. I wish I could change the nut material, but the customer only wants carbon steel. Any recommendations?
Jeff JungmannEngineer - Madison Hts, Michigan
January 6, 2010
January 11, 2010
Jeff,
Your problem is that when you are salt spraying the assemblies you have a galvanic cell set up between the zinc and whatever metal it is in contact with. This will cause preferential corrosion of the zinc at an accelerated rate.
To successfully pass the test you need to isolate the zinc from the other metal(s), alternatively you need a coating that is closer to the assembly metals (bronze, tin etc). I don't think you would be a million miles away if you were to plate with tin. As it currently stands you are almost always going to fail the test.
Aerospace - Yeovil, Somerset, UK
I agree with Mr. Terry that the current combination is likely to fail this test consistently. I would investigate a different coating, such as electroplated tin-zinc or zinc-nickel (12-15%). If you are concerned about tolerance problems with the internal threads, perhaps you could have the thread section masked or have the threads manufactured after coating.
Toby PadfieldAutomotive module supplier - MI, USA
January 13, 2010
Q, A, or Comment on THIS thread -or- Start a NEW Thread