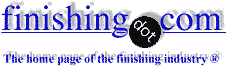
-----
Passivation Test Method Needed
Q. How can we evaluate passivation layer thickness by electrochemical method (DC corrosion test)?
Tapan K. Rout- Orissa, India
A. The answer for that is neither simple nor exact. Calculation of thickness, some graphical representations, discussion, etc., is in Electrochemical Kinetics by Vetter K.J. Academic Press N.Y.(1967) pp 759-773.
Enjoy.
Arik Lin, Electrochemist- Israel
Q. I am looking for a product or an instrumental technique that is able to determine the effectiveness of a stainless steel passivation process. There are many methods to determine whether stainless steel is passivated, but few that can determine the quality of passivation. I am looking for a method that is at least semi-quantitative so that I will be able to distinguish the quality of passivation between two different passivation methods (ie: nitric acid vs. citric acid).
Heather Johnson- St. Paul, Minnesota
2000
![]() |
A. Heather: The only accurate quantitative measure of the passivation layer is to run ESCA & AES testing on the surface. This measures the actual chemical composition of the surface, and calculates the ratio of chromium to iron on the surface, and how thick the chrome oxide layer is. There are a few electrical instruments around, but we have not found them to be accurate. We have test data that we can share with you comparing the nitric acid and citric acid systems using these tests. There are a number of test labs around the country (one in Minneapolis) that runs the tests. We can share these with you also, if you contact us. Lee kremer ![]() ![]() Lee Kremer Stellar Solutions, Inc. ![]() McHenry, Illinois ![]() 2000 A. Heather, This is a huge issue. Experience is that Electro Polishing provides the most passive film structure but even that varies from EP process to process. It is also dependent on post polishing processes being correct and not contaminating what was a clean surface. I have used every conceivable technique and am still amused by the degree of variability for every test other than the Scanning Electron Microscope. Mind you, once the EB passes over the piece it is no longer passive! SEM is just not feasible in the work shop! However, to quantify between citric and nitric is pretty easy. Simple EMF / Free Energy calcs will show you the differential in chemical activity. Remember Nitric is an oxidiser and so must be used in conjunction with a reducer such as HF. citric acid and its various formulations has its uses but does not have the solvation characteristics to deal with anything other than poorly bonded surface scales. The SURFIN 2000 proceedings contain a paper on the chemical models for this chemistry if you want further detail I would be happy to assist. Hamish Hunt- Melborne, Australia 2000 2000 A. The typical passivation tests, such as per ASTM A380 , are generally 'go-no go' types of tests. I can think of two options for a quantitative/semiquantitative evaluation. The first is an analysis of the chemical composition and thickness of the passive layer on the passivated materials. This could be done by Auger Electron Spectroscopy or X-ray Photoelectron spectroscopy. The composition, thickness and chemical state of the metal surface are good semiquantitative indicators of the passivations state. The second alternative is a corrosion test. Some sort of electrochemical test to measure the active passive behavior or pitting potential would be best. You may also be able to do some type of chemical exposure, where the time to visible corrosion signs would be your quantitative indicator. I hope this helps. ![]() Larry Hanke Minneapolis, Minnesota |
A. The ferroxyl test is a rather simple test that is quite sensitive. Depending on your needs, it may be great or too sensitive or not sensitive enough. Try it, you may like it.
James Watts- Navarre, Florida
2000
A. The Ferroxyl Test is very sensitive. I like the Koslow Passivation Tester because it doesn't require mixing chemicals. Go for the fastest method for many pieces.
Lauren KeaneKoslow Scientific Company

Englewood, New Jersey
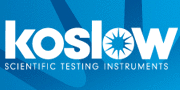
April 22, 2010
Q, A, or Comment on THIS thread -or- Start a NEW Thread