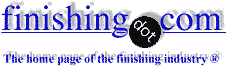
-----
Electric Connector Resistant to Sea Water Under DC Voltage
2000
My company is developing a consumer product which has to stand sea water for hours (let's say 100 hours). Unfortunately there is an electrical connector in the outside, bearing a DC voltage of 3 to 5 V. The distance between anode and cathode is ca. 1 mm, and each contact has approx. 2 square mm.
The contacts which we have used before (for non-water applications) are made in phosphorous bronze, and then a layer of nickel, and then a layer of gold. But with this voltage in sea water, the anode gets corroded very quickly. (This is made worse because the nickel has cracks which make the gold layer useless most of the times.)
Our search for solutions is made harder by the fact that we need very low electrical resistance of the contacts, because they are used to power a external accessory. Furthermore, it should stand like 30.000 connect-disconnect cycles (probably graphite is too soft). Besides, it must be feasible for high-volume production (and then, platinum is probably out of the question because of price, I guess?).
I would appreciate any suggestion. Thank you.
Ignacio UrrutiaIndelec - Zamudio, Bizkaia, SPAIN
Why not try High phosphorous Electroless Nickel instead of plated Nickel? May give you the hardness needed for many operations as well as corrosion resistance. I don't know if you can plate gold over it although.
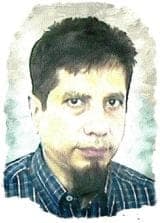
Khozem Vahaanwala
Saify Ind

Bengaluru, Karnataka, India
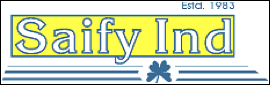
2000
I think you will need another kind of contact altogether.


Tom Pullizzi
Falls Township, Pennsylvania
2000
Hi all,
I want to point out that our former solution stood all the mechanical and electrical requirements (low resistance, 30k cycles, etc.), except for the immersion in salt water.
Khozem, do you have any idea of how thick should the layer of electroless Nickel to work OK?
Tom, do you have any suggestion about the composition of this completely new kind of contact?
Thanks a lot and best regards.
Ignacio UrrutiaIndelec - Zamudio, Bizkaia, SPAIN
2000
25 microns should be enough. But you will have to determine this yourself with practical tests. regards.
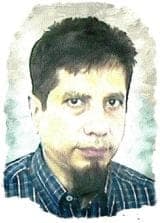
Khozem Vahaanwala
Saify Ind

Bengaluru, Karnataka, India
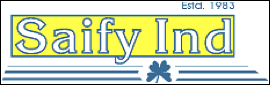
2000
Q, A, or Comment on THIS thread -or- Start a NEW Thread