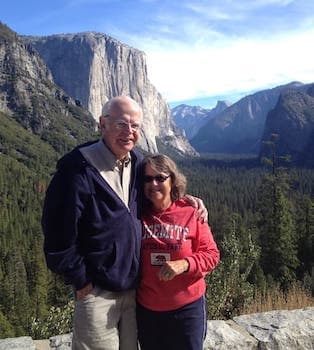
Curated with aloha by
Ted Mooney, P.E. RET
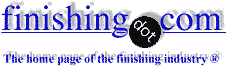
The authoritative public forum
for Metal Finishing 1989-2025
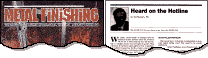
-----
Aluminum anodising questions: titanium rack stripping, anode to cathode ratio
Q. I have a few questions about sulfuric anodising process of aluminium. We use titanium jigs for electrical contacts. I was wondering about the resistance of the formed oxide film on these jigs. Is it very resistant and do we have to clean them before each anodising bath? We also use a lead-lined tank. Is there any ratio cathode.anode and are we allowed to put any size of aluminium parts to be anodised. Is there a limit?
Cedric Ody- Dublin, Ireland
2000
Treatment &
Finishing of
Aluminium and
Its Alloys"
by Wernick, Pinner
& Sheasby
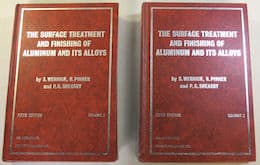
(note: this book is two volumes)
on eBay or
AbeBooks
or Amazon
(affil links)
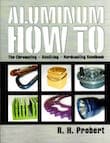
Aluminum How-To
"Chromating - Anodizing - Hardcoating"
by Robert Probert
Also available in Spanish
You'll love this book. Finishing.com has sold almost a thousand copies without a single return request :-)
A. The oxide that forms on titanium racks is minimal in resistance if you routinely clean your racks in your sulfuric acid bath. Do the following:
Clean the racks in your cleaning solution, the whole rack. To remove surface oils and other buildup from the shop you might have. If you have aluminum hooks attached to the racks to hand them on your flight bars. Etch these hooks in caustic soda ⇦liquid caustic soda in bulk on Amazon [affil link] to eliminate all oxides on them. Then finally, hang the entire rack into your sulfuric acid for the night. In the morning, all built up oxides will be removed and you'll have nice, clean new racks to work with. My honest suggestion is at most every 2 weeks, but every month should be just fine for most persons. If you make it a routine monthly thing, sooner or later you won't even have to question whether it works or not.
As far as cathode to anode ratio: 1:4 is the ratio I see everywhere if not mistaken. I don't believe its 4:1, that just doesn't sound right. So therefore, you have 4sq. ft of surface area anode wise, you have 1sq.ft of cathode surface area. To measure the cathode surface area you take the part facing into the tank, get its total dimensions and divide by 2, then add 10%. That is a safe estimate from Dr. Kushner, because you actually don't have 100% surface area positioned towards your part, you have 50%, 100% would be both sides of the cathode, and thats just not the case, the extra 10% is for the possibility that the sides and a minor portion of the back does actually migrate into the tank to be useful in the process.
Is there any limit to the amount, size wise you can put into your tank? Thats dependent on your cathode surface area, and your rectifier capacity. If you have 3,000A possible on your rectifier (as I do on one of mine). Standard sulfuric @ 12A/sq.ft would allow for approximately 250 sq. ft of surface in the tank before you maxed out your rectifier. Then you would have to have 62.5 sq. ft of cathode surface area to ensure that you're capable of generating the 12A possible. If you only had 50sq. ft of cathode you'd essentially be pulling 9.6A/sq ft if I'm doing my math right. Thats not to say that you can't push more through the cathodes than 12A, thats not the case. I use lead cathodes myself, 30-50A/sq ft is entirely possible, but for examples sake I think my point is valid. Again, for example if you went with 14A/sq ft instead of 12A, the tank could only hold 214 sq.ft before it maxed out the rectifier. I myself take 10% off that # for the fact of loss due to heat losses in the bar, and possible losses due to other factors in the process, its a very safe cushion, that more than allows you to stay within your boundaries.
I hope I've answered some of your questions. If anyone cares to correct a glaring error I have made, feel free to. If you need some further insight, feel free to respond back, good luck to you Cedric.
Matthew Stiltner- Toledo, Ohio
2000
Q. Question on the response re cleaning titanium racks... when you say leave the racks in the sulfuric acid bath overnight, do you mean the sulfuric acid anodize bath?
David A. Kraft- Long Island City, New York
2000
Q. Thank you for your answers. I am working on my cathode. We used to have a lead tank so the current was too high for a small part of aluminium. I have done some tests with aluminium but the results I get are much better than before but I don't manage to get a accurate current density of 15 Amps/sq ft.
I wonder if the cathode for your calculations has to be stuck to the plastic tank or left in the tank in order that the two sides work during the process.
My second question is how do we do if the total area of aluminium changes along the day. Do we have to keep the same area each time we anodise. Are there some limits.
My last question is : does it change to use lead or aluminium cathodes in the calculations.
Thank you very much. You help me a lot. Cedric.
Cedric ODY- Dublin
2000
A. David:
Yes I mean the sulfuric anodize bath, unless of course you have another sulfuric tank that you don't anodize out of. Either of them will work, just don't apply current and when you come in to work in the morning, you have clean racks. Again you don't have to do this every night, the oxide on the titanium builds up so slowly that once every 3-6 months should be adequate for most persons.
Cedric: As far as my calculation goes, those are dependent upon the fact that you'd have the cathodes attached to the sides of the tank. You can add a few more % points if they are not placed against the side, but it is nothing overly dramatic to where it would make for a large difference in calculations.
Answer for Question 2: If you anodize the same parts over and over again, in 25 pieces per load, everything should stay constant, your voltage, your amperage, essentially nothing should change for what you should do in the process. If you are constantly doing different parts on a daily basis (who isn't, we're all jobshops around here). Then you have to compensate for the changes in load sizes.
12A/sq ft on 100 ft is different that 12A/sq ft on 50 ft, instead of 1200A per load you have 600A. Also the fact that because of the material composition you may have to adjust the voltage up or down dependent upon the material, some take more voltage to anodize to the same thicknesses as others. I never anodize 2024 material, but I do believe it takes more than 6061, voltage wise to achieve the same ASF and thicknesses in relation to that.
Matthew Stiltner- Toledo, Ohio
2000
![]() |
Q. Dear Sir/Madam, Just a quick question. Talking about aluminium anode, usually what you can see in the supplier's brochure is only specifying the effective amount of electricity of anode. What about the average anti-corrosive electric current density? Is this not important when the user sources for an aluminium anode? Also, have you any idea about what MF-34 aluminium anode is? Thank you in advance. Regards, Pei Chen Lau- Petaling Jaya, Selangor, Malaysia 2001 Hello Pei There is a company that offers model no MF-34 anodes for protection of ship hulls, and I think your question is referring to sacrificial anodes for ships rather than the aluminum anodizing that we speak of on this industrial metal finishing site. Sorry, but I and most of our readers know nothing about your topic. Good luck. Regards, ![]() Ted Mooney, P.E. Striving to live Aloha finishing.com - Pine Beach, New Jersey |
The Sulfuric Acid Process"
by David LaPlantz
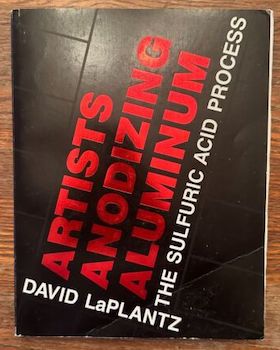
on AbeBooks
or eBay or
Amazon
(affil links)
by S. Kawai
on AbeBooks (rarely avail.)
or eBay
(rarely avail.)
or Amazon
(rarely avail.)
Wasn't available from any of these sources last time we checked, but we'll maintain the links in case a copy turns up :-)
(affil links)
Q. Can you please help me understand the solution ratio used for 300 sq inches of surface average of Al to anodize?
Miguel Martin- Mexicali, Mexico
2006
A. Hi Miquel.
I personally have never heard of a limiting solution ratio for anodizing. Rather, I think if the parts conveniently fit in the tank, then the tank is big enough. But anodizing does require cooling, and if you are not providing refrigeration, I think even a fairly large tank can overheat quickly. In fact the ambient temperature in Mexicali probably exceeds normal anodizing temperatures of about 68 - 70 °F (20 °C).
Regards,
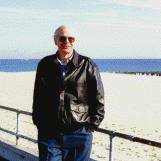
Ted Mooney, P.E.
Striving to live Aloha
finishing.com - Pine Beach, New Jersey
July 2012
Q. Hi everyone,
For the past 2 years, I have been anodising small aluminium parts using a titanium rack that is approximately 8 to 10 times larger that my workpieces in terms of surface area. I use a current density of about 1.8 A/dm2. Usually I don't account for the rack area in calculating current.I am wrong in doing so?? Should the area of the rack also be considered when calculating current?? I've been getting very inconsistent results lately...please help...
- Goodlands, Mauritius
November 14, 2013
A. While titanium does not require stripping as much as aluminum racks do, eventually much of the contact point becomes anodized which will limit the amps/volts to some of the parts, leading to inconsistent product.
The rack does not draw that much current after 3 to 5 runs with it so at that point, you MIGHT not need to consider it. The first couple of runs after stripping, it would be a factor!
Have you considered masking off part of the rack?
- Navarre, Florida
November 14, 2013
Q. Thanks for your response James, I really appreciate it. Would you please advise of some ways of masking the rack? I tried in the past with organic lacquers but the coating eventually strips off some in a couple of runs.
Ruben Chinapiel- Goodlands, Mauritius
November 18, 2013
A. A good stretchy vinyl tape is the easiest to try, Seal the ends with an electroplating lacquer.
Plastisol is a bit harder to apply. It needs a clean preferably blasted surface and the appropriate primer. It requires an oven that you can get dirty and it is not as easy as it sounds--i.e.: a learning curve.
There are some vinyls that work reasonably well and some come in spray cans.
One that I used was a stretchable maskant-Super XP 1000 from pyramid plastics. If applied over an abrasive blasted rack and dried at 140 °F it was very difficult to get off, which is desirable for rack masking.
- Navarre, Florida
November 18, 2013
Q, A, or Comment on THIS thread -or- Start a NEW Thread