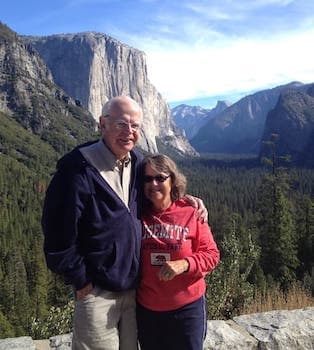
Curated with aloha by
Ted Mooney, P.E. RET
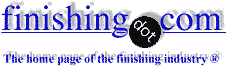
The authoritative public forum
for Metal Finishing 1989-2025
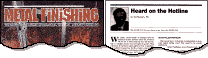
-----
Corrosion of anodized 6063 Aluminum alloy and solutions.
Hello.
I have been involved in this project where 6063 Aluminum alloy wall frame on the building shows some corrosion damage. It has been only around two years since the initial installation, and it was reported that some kind of deicing agent has been used during the installation because it was during cold winter. Lab data shows that chemical composition of the corroded material is mostly of aluminum and chlorine. So, I assume the corrosion attack is done by environment or other influencing chemical containing chloride ion. But, it was reported that it has been through anodized finish before installation.
Is it common or normal that aluminum alloy such as this with anodized finish can have corrosion in such a short (or reasonably short) period?
In addition, the corrosion damage is shown at the bottom of frame and the joint of frame with localized pitting appearances. So, I am guessing it may have been caused by the stagnation of moist or other liquid forms of chemicals at the bottom of frame and some kind of material disruption by welding or jointing between the frames. Are my guesses right?
If so, can anyone give a comment as solutions to this problem in any level of manufacturing, installation or maintenance?
Engineering Consultant - Irvine, California
December 29, 2009
First of two simultaneous responses -- December 30, 2009
The damage could have been caused at any of the points that you mention.
Anodize that is properly prepped and applied, including the proper seal, should last longer than two years, unless there is something in the atmosphere or is "cleaned" with that would shorten that time.
Having no hard facts to go by, no one will be able to do any thing but guess, and that falls in the realm of the unkind meaning of
"assume".
- Navarre, Florida
Second of two simultaneous responses --
Free chloride,as in salt containing de-icers, attacks, aluminum, aluminum oxide (anodizing), and hydrated aluminum oxide (sealed anodizing). Simple. conventional anodizing is not suitable for outside exposure, particularly in sulfur bearing industrial neighborhoods and anywhere that salt deicers are sprayed on. "Architectural" anodizing on mill special alloys in very special electrolytes hold up well in outside exposure. You should lightly chromate conversion coat and apply powder coating paint.
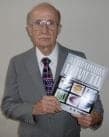
Robert H Probert
Robert H Probert Technical Services

Garner, North Carolina
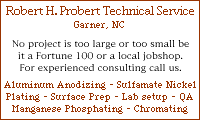
December 30, 2009
Q, A, or Comment on THIS thread -or- Start a NEW Thread