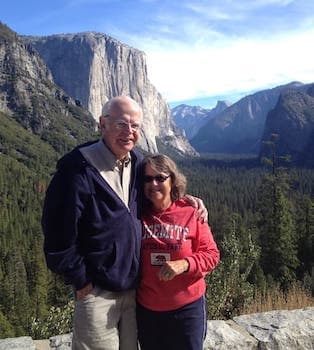
Curated with aloha by
Ted Mooney, P.E. RET
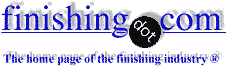
The authoritative public forum
for Metal Finishing 1989-2025
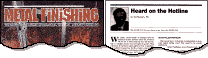
-----
Need formula to give hardness of up to 1050 to a copper-based print cylinder
December 16, 2009
Respected Sir
I am working in a cylinder making company for packaging. We tried our best to give chrome hardness to the printing cylinder up to 1000. but maximum I can reach up to 950. please suggest me what should I do to give printing cylinder chrome hardness up to 1050. please tell me the formula in details.
thanks and regards
Plating shop employee - 6th of October, Gija, Egypt
![]() |
No one is giving free formulas. ![]() ![]() Sara Michaeli Tel-Aviv-Yafo, Israel December 20, 2009 A hardness of 1050 is pretty difficult to get with hard chrome. I would suggest you consider using a titanium nitride (or even chromium nitride) treatment; this is different to electroplating as it is vacuum deposition, but it will give you a harder coating ![]() Trevor Crichton R&D practical scientist Chesham, Bucks, UK December 21, 2009 |
December 21, 2009
Is this on a copper cylinder or on a copper coated steel cylinder?
Why do you think that you need 1050 hard chrome? That takes some really tight parameters that are tough do keep when plating large cylinders. It is difficult on even lab sized setups.
Look up "micro discontinuous chrome" and see what you can find. It used to all be proprietary, so the information available was minimal and protected. They claim unreal high numbers such as what you are looking for. PS: the cost is high!
- Navarre, Florida
Guys, don't confuse Ashraf with technologies that were never used for his application.
It is a very special application which has a known process.
There are special solutions used for the copper and chrome in this field.


Sara Michaeli
Tel-Aviv-Yafo, Israel
December 23, 2009
December 23, 2009
Hello,
Please consider that a higher chrome hardness will not result in better running time and better printing results. The make of the cylinder is as well very important as well as the printing parameters (doctor blade angle and pressure, oscillation method; type of substrate and inks in use; printing speed and printing machine setup (tension of substrate during printing process, temperatures etc). Quality of the copper deposit and the choice of the right engraving parameters also improves the durability and quality.
If you do not use until now an catalyst in your chrome solution, I would suggest you add an additive which is available at the Provider side in the Rotogavure Industry. Also an review of your process (copper, chrome, temperatures, current density etc) would be recommendable and is in most cases free of any costs if you buy the additives from your providers.
Good Luck,
- Australia
Q, A, or Comment on THIS thread -or- Start a NEW Thread